June 17, 2024
Once again this year, around 50 students from Karlsruhe University of Applied Sciences (HKA) came together to design a single-seater formula racing car and then build it themselves. They come from the degree programs Automotive Engineering, Mechanical Engineering, Mechatronics, Electrical Engineering & Information Technology , Business Administration & Engineering, Computer Science , and Computer Science & Media , and had a common goal: To build their own racing car for this year's participation in the international student design competitions of "Formula Student". As in the previous year, the team will take part in three different international competitions: in Spielberg in Austria, on the ZalaZone test track near Zalaegerszeg in Hungary, and on the Hockenheimring.
After nine months of development, design and production, the students had now reached another major milestone with the rollout on Thursday, June 13, 2024, and were able to present the result of their project work to the public for the first time with the new "F-118" racing car.
The main task of the international Formula Student design competitions is to produce a racing car that would be suitable for small-scale production. However, speed is only one aspect; the overall concept is evaluated, which also includes acceleration and braking performance as well as design, weight and calculated production costs. In order to develop a fast, agile, safe, economical and reliable racing car that is also cost-effective, the students need to plan and coordinate the project in detail, including a marketing strategy, business plan and cost report. This requires many engineering-specific skills, as well as extensive business and marketing skills. The idea behind this competition is to give students an attractive opportunity to put the knowledge they have acquired during their studies into practice.
This season, the team is competing with a purely electric vehicle for the first time in more than ten years. In addition to the carbon fibre (CFRP) body, which has been made lighter thanks to an optimized layer structure, there is also an improved braking system with brake calipers developed in-house. In order to optimize the flow conditions on the vehicle, many more time-consuming computer-aided simulations were carried out, resulting in a more complex aero package with partially active aerodynamics compared to the previous year's vehicle. This includes a new underbody, covers on the transverse links and new SLS-printed cooling elements (3D printing technology that allows internal shapes to be printed without support structures). More adjustment options and new end plates on the rear wing are intended to provide more downforce while reducing driving resistance.
The drivetrain is powered by an all-electric rear-wheel drive with a maximum output of approx. 75 kW. The two wheel hub motors and gearbox are integrated directly into the wheel pack. The torque is transmitted via a 1½-stage planetary gearbox. The high-voltage battery in an aramid housing consists of 12 modules - a total of 432 round cells - and has a maximum voltage of 600 V.
New acceleration sensors, GPS support, new onboard electronics and zone architecture enable a more comprehensive, more stable and more precise evaluation of the driving data during the test phase and during competitions.
As in every modern development and production process, the complete vehicle is first created as a model in the computer using CAD (Computer Aided Design) systems. This not only creates the required production data, but also enables the simulation and calculation of the various components and functions. The components are then individually manufactured and in some cases tested until they are destroyed.
There is hardly any other project where the basics acquired in lectures and exercises can be put into practice as comprehensively as in this Formula Student project. All the necessary steps are organized by the students themselves, right up to the highly complex production of the individual parts. They are supported by many sponsors and by the workshop of the Faculty of Mechanical Engineering & Mechatronics, where a large proportion of the required components are manufactured in-house.
After the rollout of the "F-118", the short test phase begins for the students in order to make the car fit for the Formula Student competitions. At the end of July - shortly after the end of the exams that the students involved in the project still have to take - they will then "really get going" with the first competition event in Austria.
"For us, the students' racing car, which is developed further every year, is always impressive proof of the combination of specialist knowledge and the pronounced practical relevance of our teaching and also of how well our students manage to plan and implement such an extensive project," emphasizes Prof. Dr. Rainer Neumann, Vice-President for Academic Affairs at HKA.
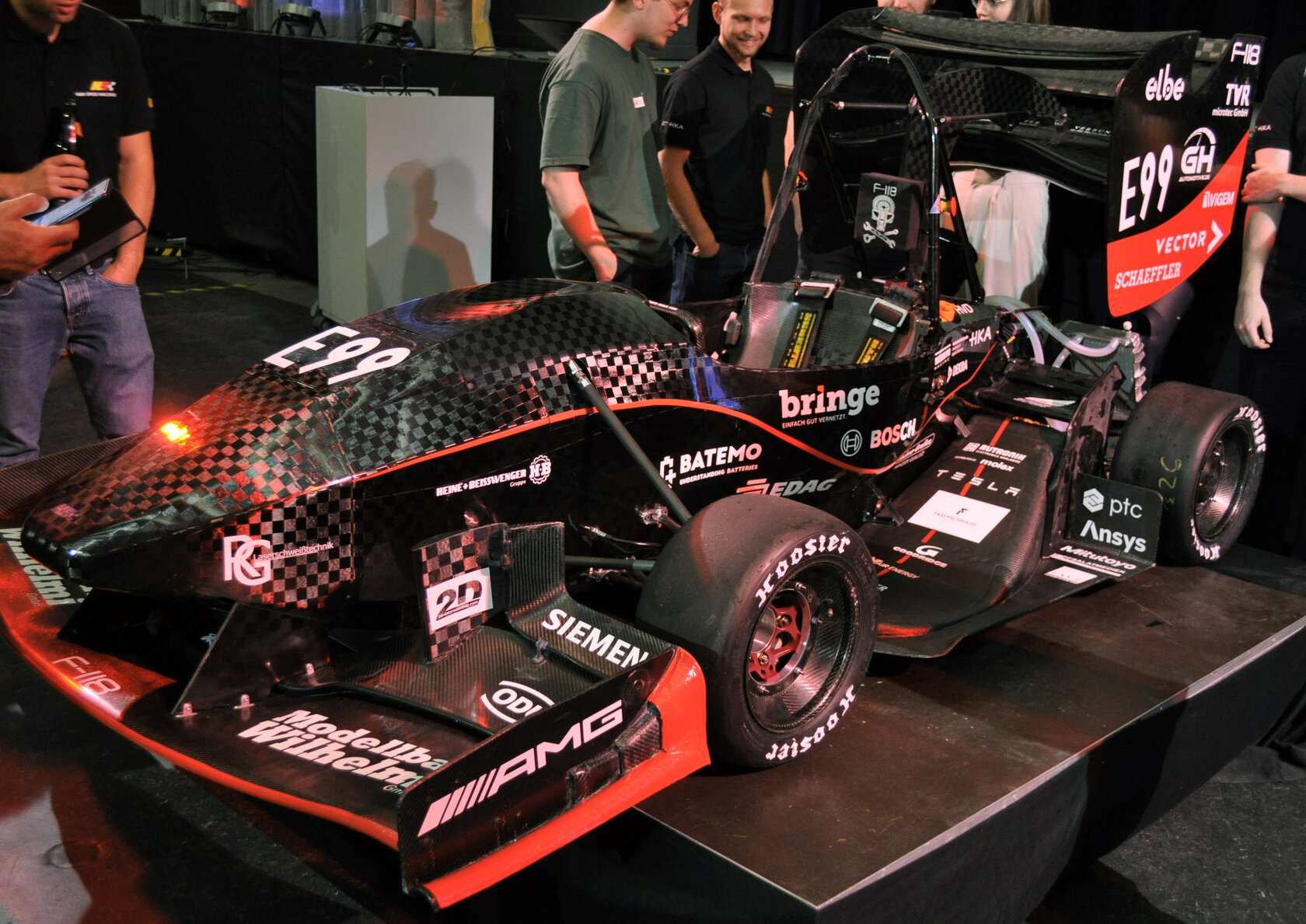
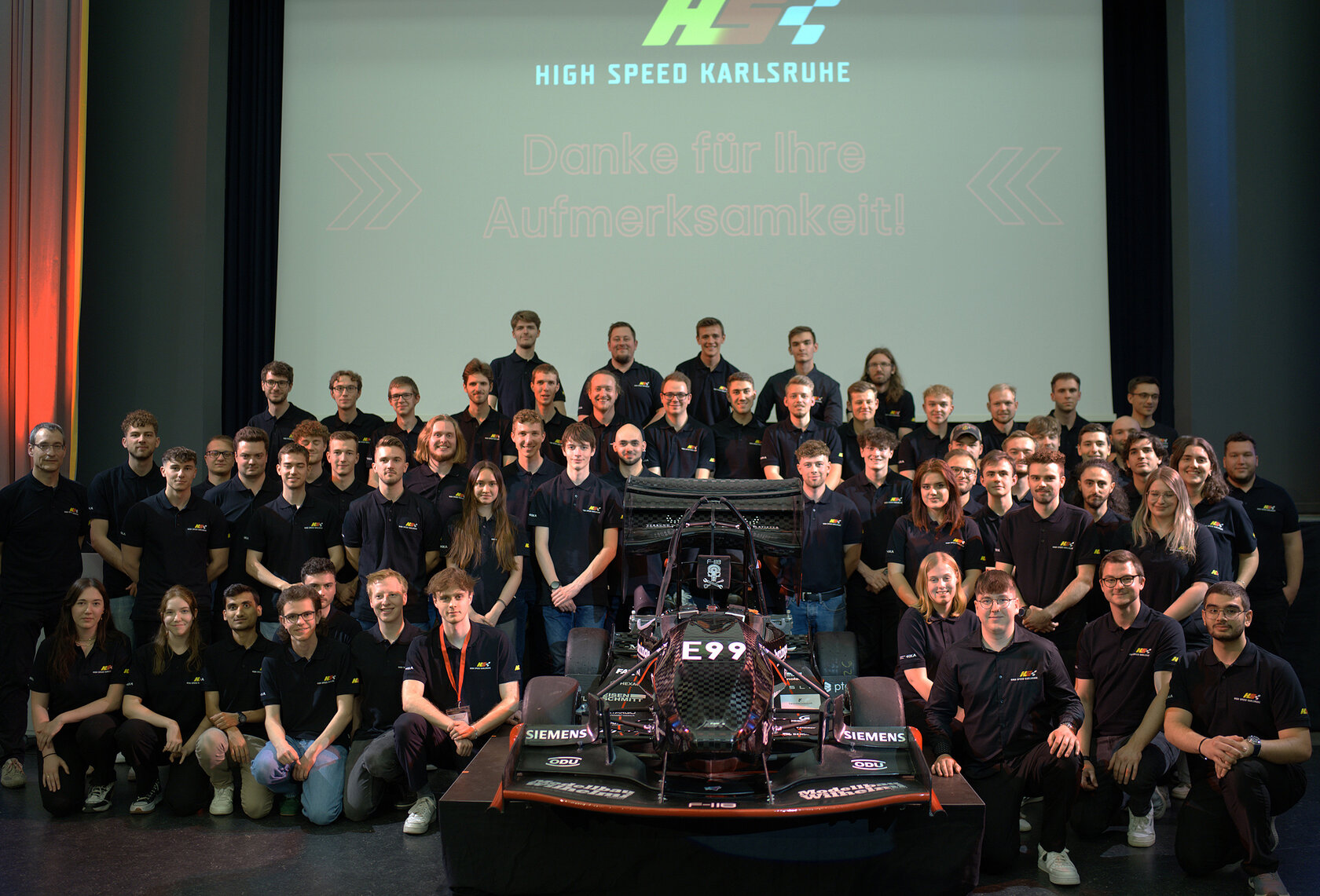
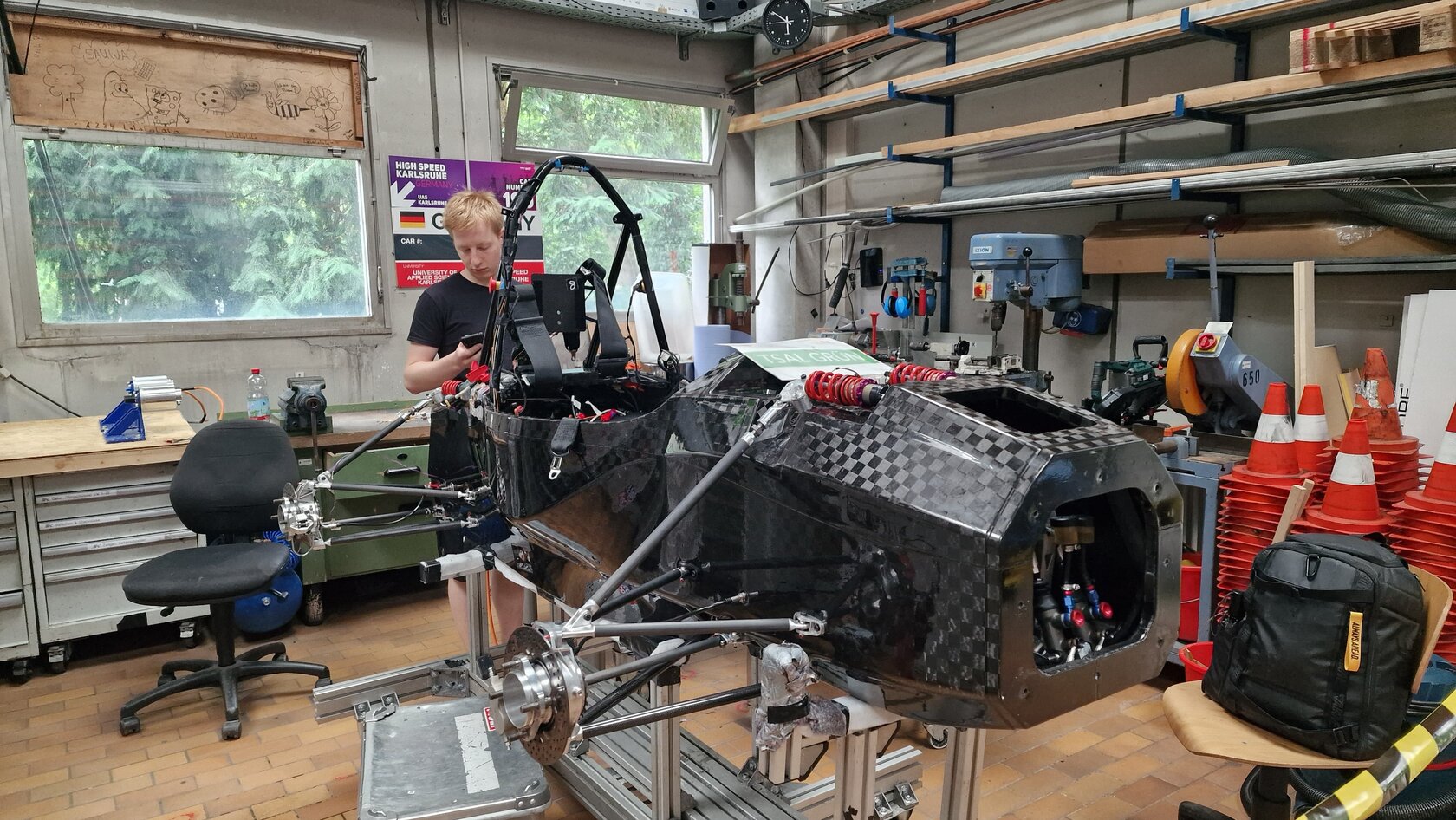
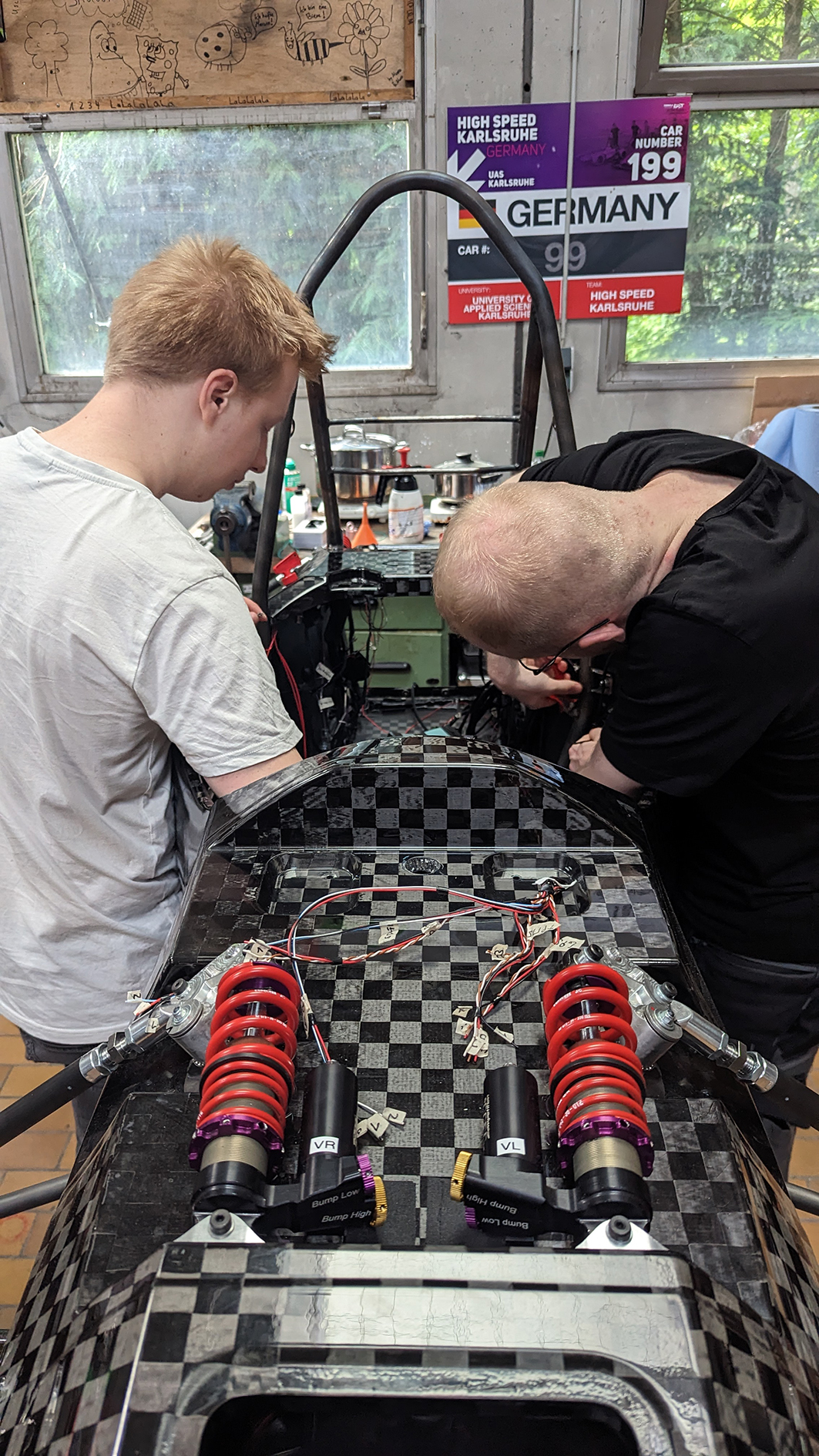