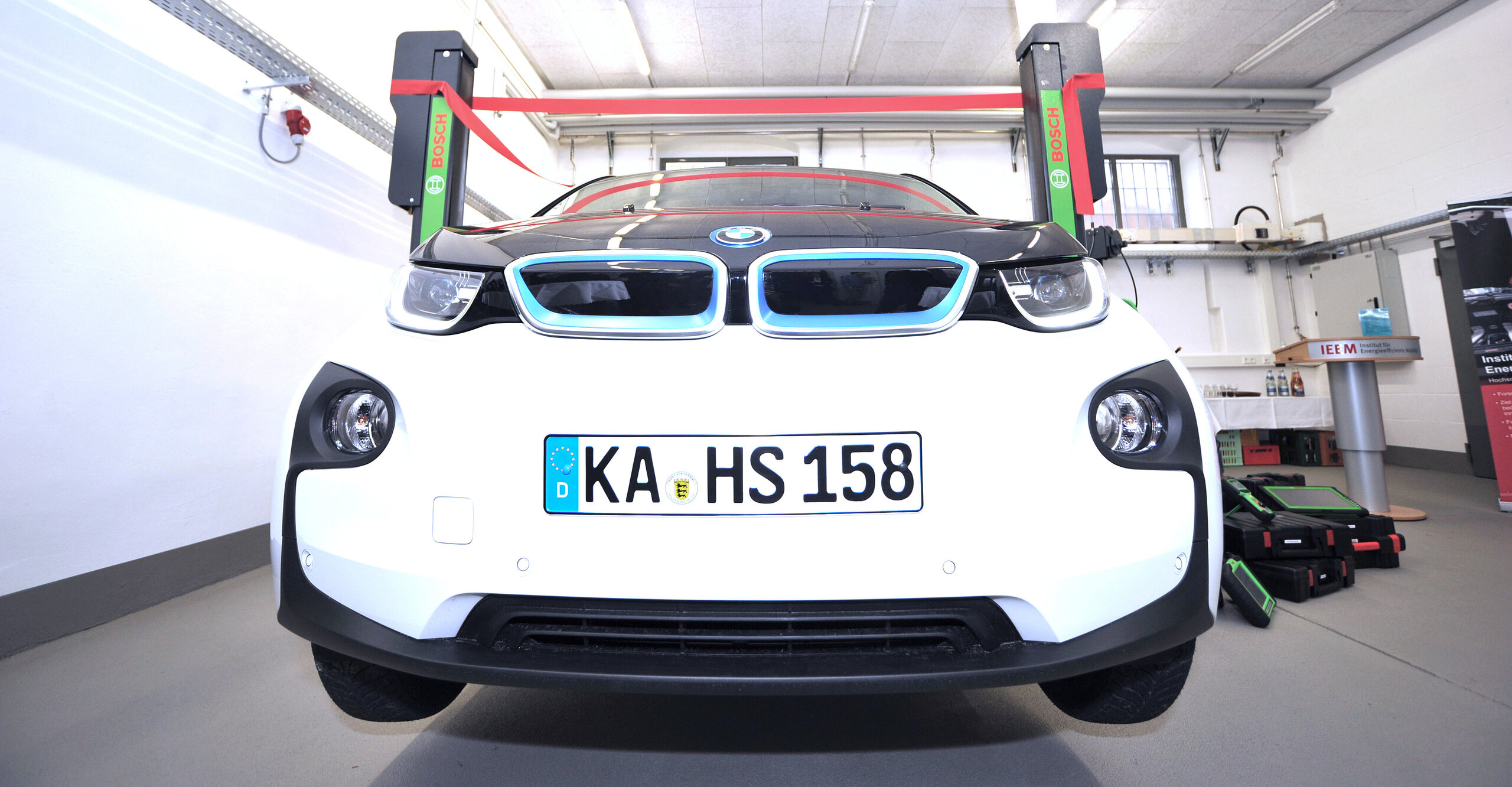
Automotive Mobility Lab
The Automotive Lab offers a wide range of virtual and physical measurement and test benches as well as simulation platforms. These include:
Physical test benches and workshop of the Automotive Mobility Lab
Virtual simulation and test benches of the Automotive Lab
Karlsruhe
Institute of Energy Efficient Mobility (IEEM)
Moltkestr. 30
76133 Karlsruhe
Post >
Institute of Energy Efficient Mobility (IEEM)
Postfach 2440
76012 Karlsruhe