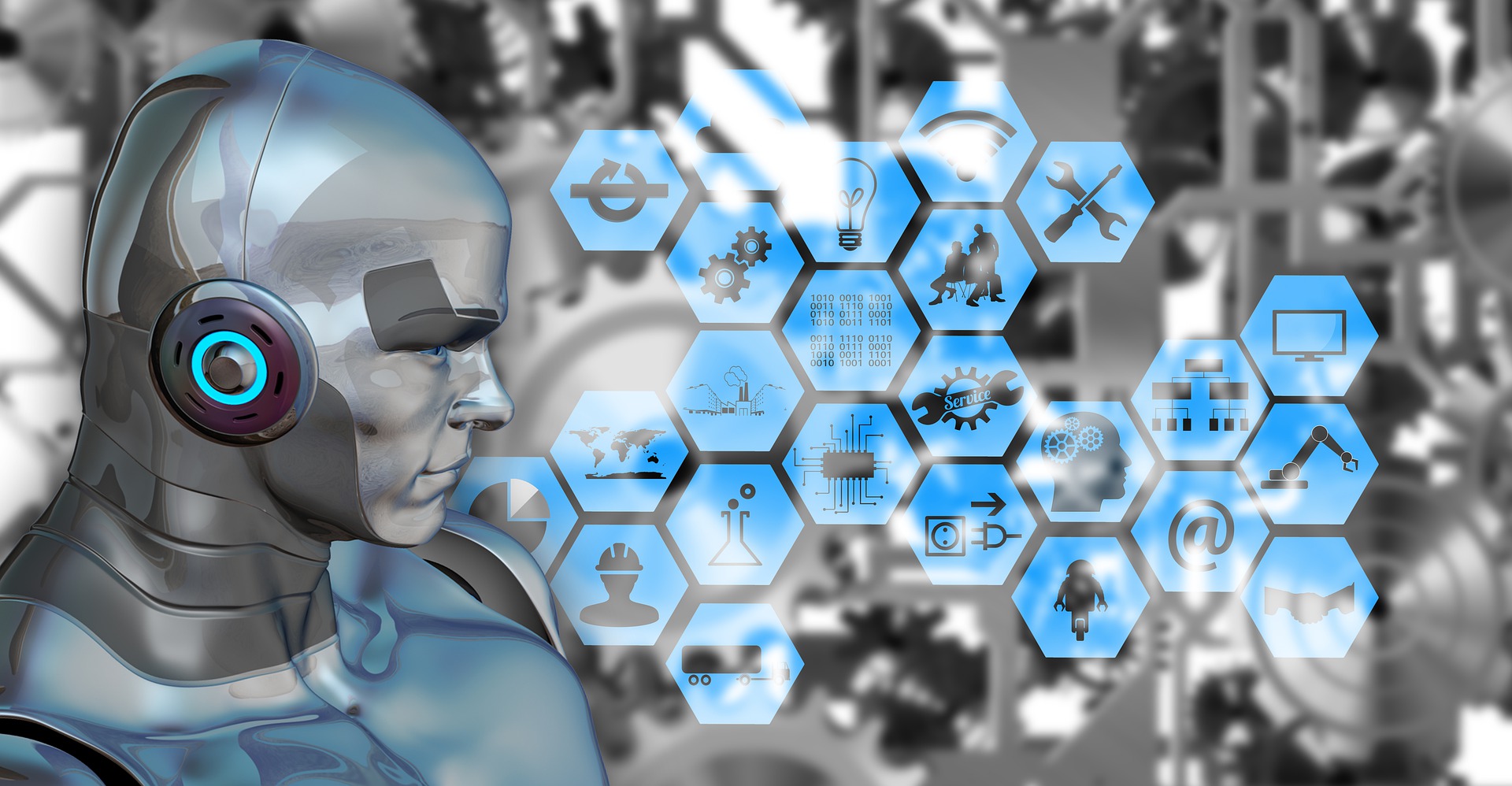
KI5GRob
Cloud computing and 5G as enablers for new sensor technologies in robot-based production and logistics
Context
Intelligent and autonomous robot-based production and logistics systems will play a central role in Germany's competitiveness. The fusion of cloud technologies and AI with the robotics of the production and logistics world is considered one of the key concepts for the implementation of such systems. Utilizing advanced cloud concepts in conjunction with 5G technology, cloud, and on-site robotic systems can be tightly coupled in real-time.
Project goals
In order to advance the fusion of cloud technologies and AI with robotics in the production and logistics world, the project KI5GRob focuses on three research questions in particular and develops suitable solutions:
- What are suitable AI methods for multimodal sensor signal processing and interpretation for the flexible use of robots in handling tasks in production and logistics?
- Which software and hardware architecture or communication infrastructure is suitable to provide and use such modern computationally intensive planning and AI methods in combination with robots easily and in real-time in terms of novel CaaS concepts (Control as a Service)?
- What are the implications of using architecture and AI practices for developers, integrators, and operators, and how can a clear, usable design be achieved?
The flexible robot-based handling, i.e. grasping and especially targeted placing, of many, highly varying objects is still an unsolved problem in logistics due to its complexity. Therefore, this will serve as a demonstrator and evaluation in KI5GRob.
KI5GRob hereby addresses how machine learning can be efficiently used in robotics in a new way, by closely linking cloud technologies and robotics in a tight control loop and how the concept pursued can fundamentally simplify the programming and maintenance of robot systems. The solution of the above questions holds great potential for the future realization of autonomous intelligent robot systems for application in production and logistics.
Methods
Compared to the state of the art the project has a high level of innovation due to the novel combination of scientific methods from the fields of cloud computing and AI methods with real-time connection via 5G to robotic systems.
The use of tactile proximity sensors in combination with 3D image processing for the research and development of new AI-based pick-and-place strategies is investigated in the scope of the project. A mobile robot of the Robogistics-Lab equipped with a manipulator, camera, and gripper will serve as a physical demonstrator for this purpose.
In addition, research will focus on providing computing power and data storage in the cloud, required for AI procedures as well as the cloud infrastructure that enables the use of AI procedures and robot control in real-time via 5G for mobile robots. To demonstrate the designed architecture concepts first, the lab (stationary robot, commissioning system) and the previously used mobile robot system are equipped with 5G communication components and connected to the planed GPU computer and the cloud computer of the Robogistics-Lab .
Status
Ongoing project 11/2020 — 04/2025
Project consortium
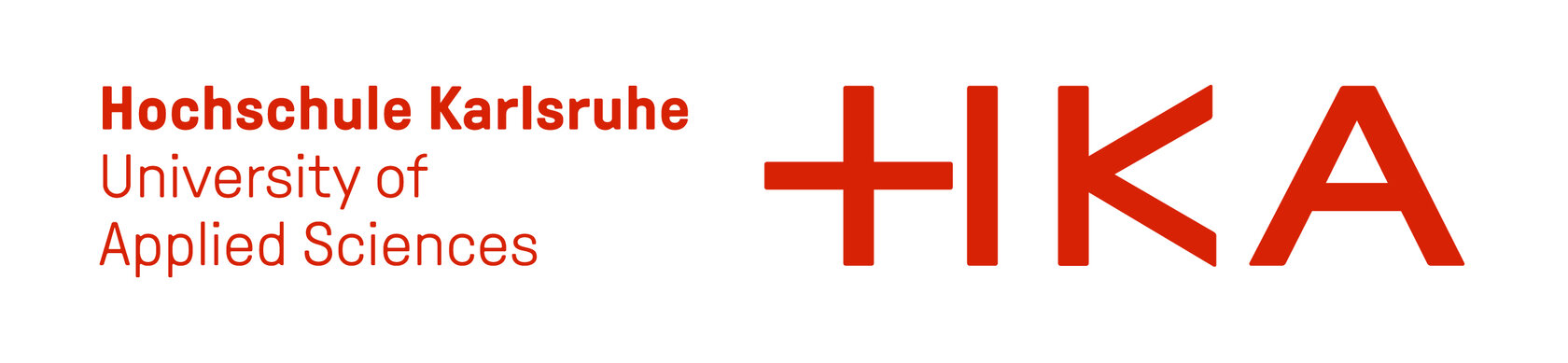


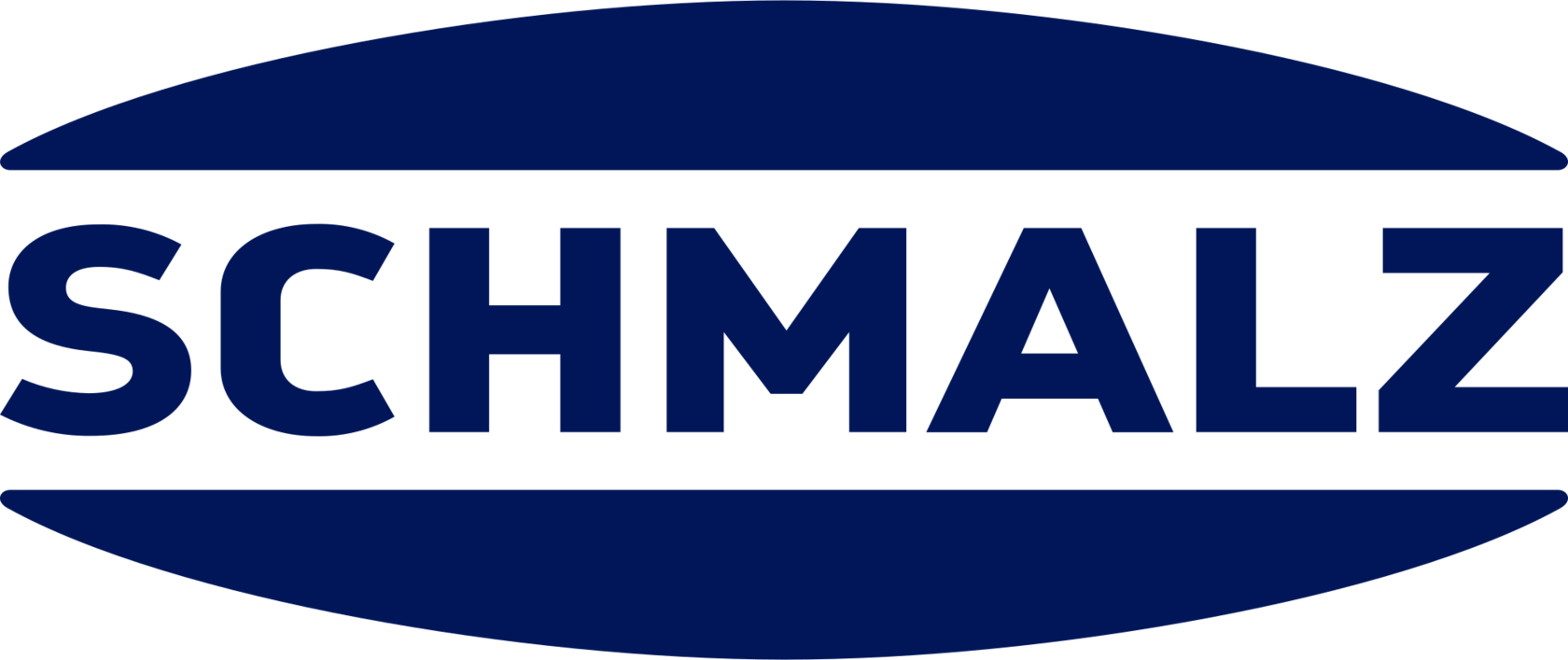
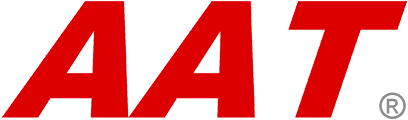
This project is funded by
The KI5GRob project is funded by the Federal Ministry of Education and Research (BMBF) and KUKA Deutchland AG as part o the funding line "Research at Universities of Applied Sciences"
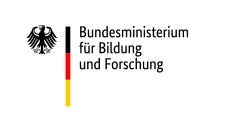
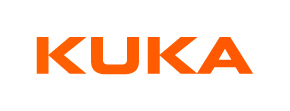