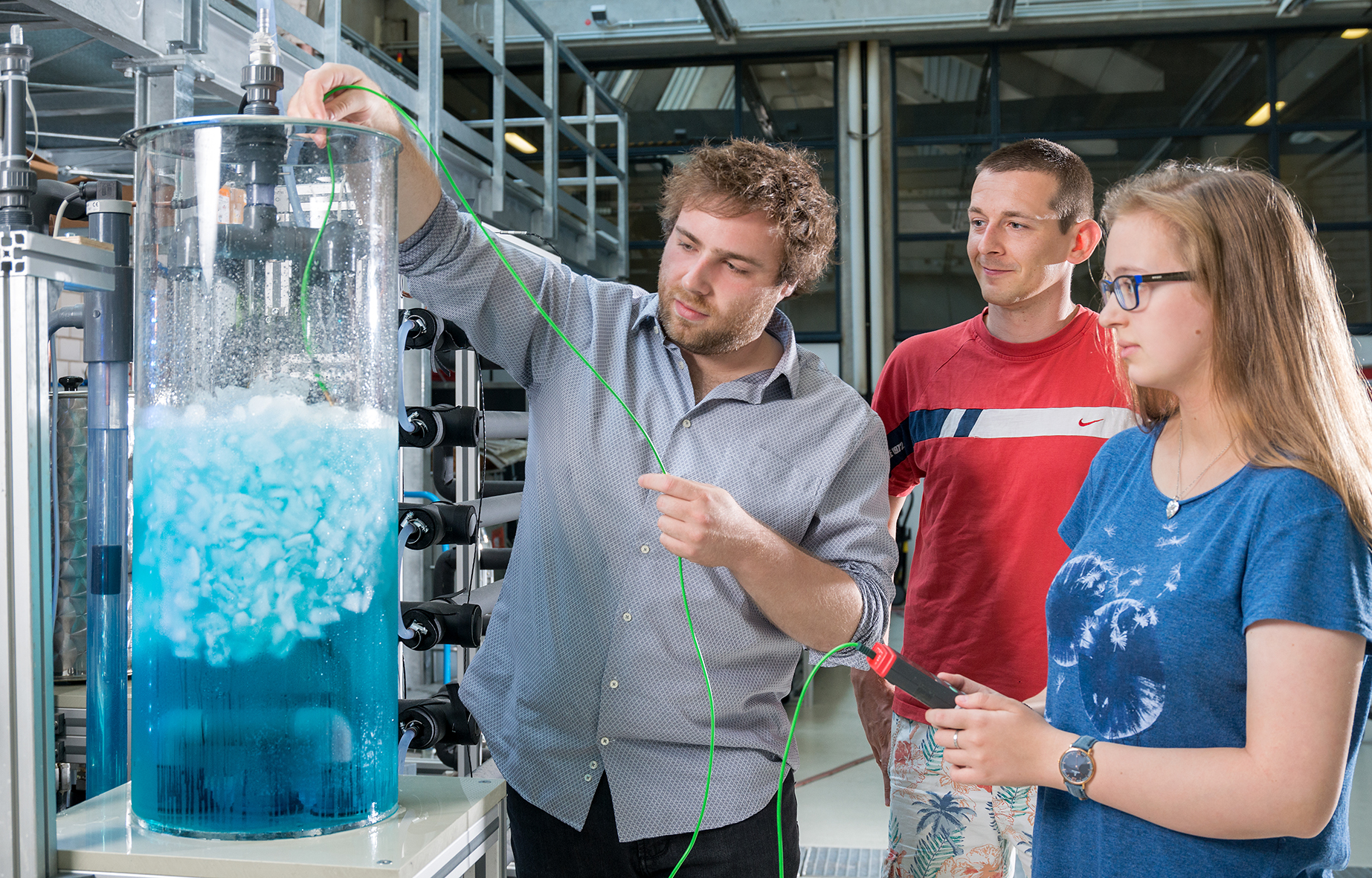
Laboratory for chillers and heat pumps
Laboratory for chillers and heat pumps
Das Labor für Kältemaschinen und Wärmepumpen besteht aus einer Reihe von anspruchsvollen Experimenten aus allen Bereichen der Kältetechnologie, die in der Regel in Gruppen von jeweils zwei Studierenden bearbeitet werden, sowie einer begleitenden Seminar-Reihe, in der jeder Teilnehmer des Praktikums jeweils eines der Experimente vorstellt.
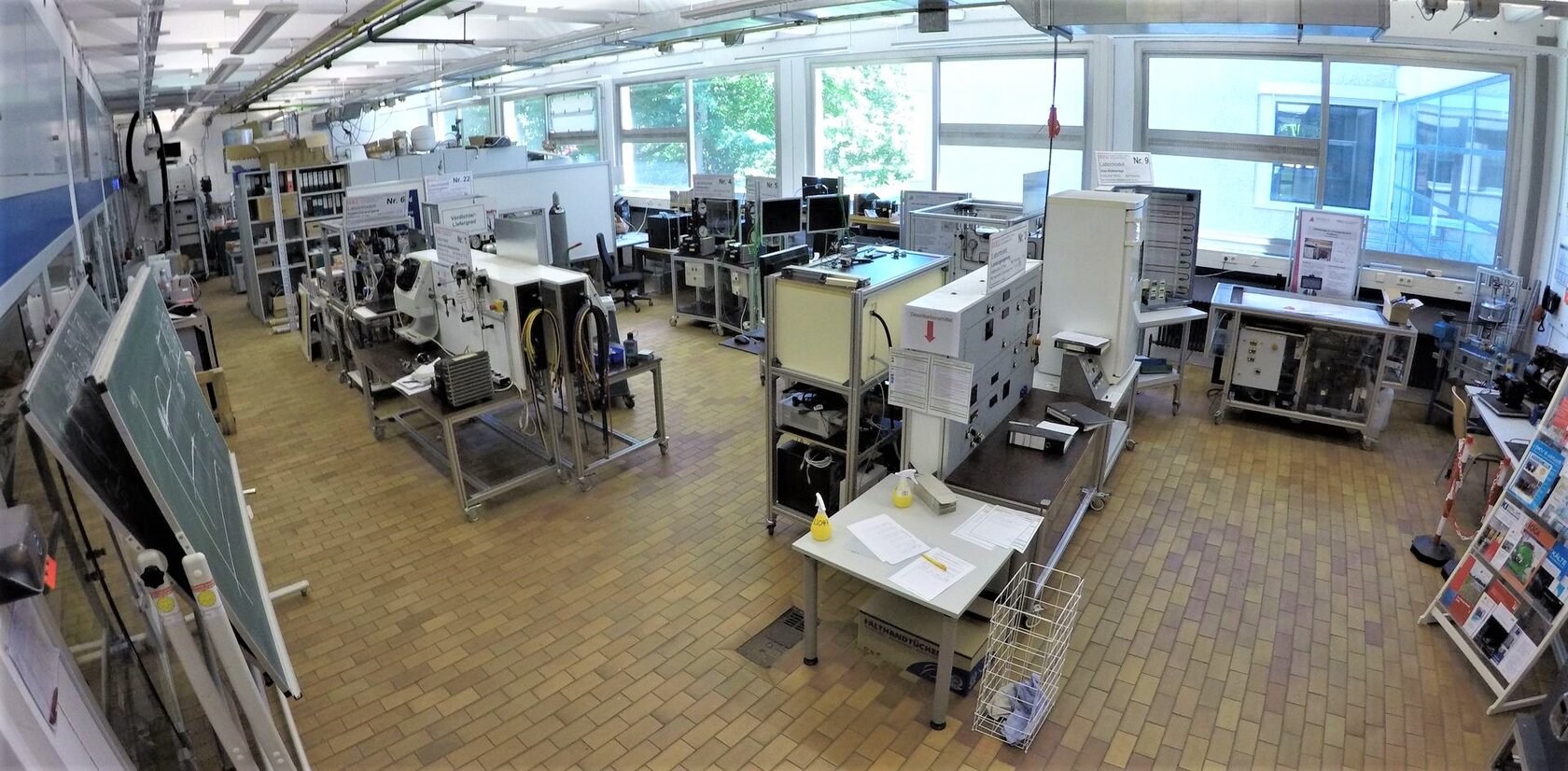
Facilities for student training
Construction and commissioning of a single stage refrigeration system
Troubleshooting refrigeration system
Refrigeration system with different expansion elements
Cascade deep-freeze refrigeration system
Power control on refrigeration laboratory model
Refrigeration system with glass heat transfer
Propane plant for demonstration purposes
Demonstration air conditioner

Construction and commissioning of a single-stage refrigeration plant
The goal of this experiment is that students
- set up a simple refrigeration system
- check for leaks
- select and equip appropriate temperature measurement points
- evacuate the system and charge it with refrigerant
- start up the plant and record some suitable measuring points

Troubleshooting refrigeration system
In this experiment, students will learn the basics of the compression refrigerant cycle in a practical way.
By systematically manipulating the refrigerant circuit, the appearance of the system present in "normal operation" will change. Students will be asked to determine the exact cause of the change in condition.
For a systematic approach to troubleshooting, it is necessary to explore the refrigerant circuit of the plant first with all senses and then by measurements. Together with theoretical knowledge of the interrelationship of the components, these observations enable conclusions to be drawn about the cause of the error.
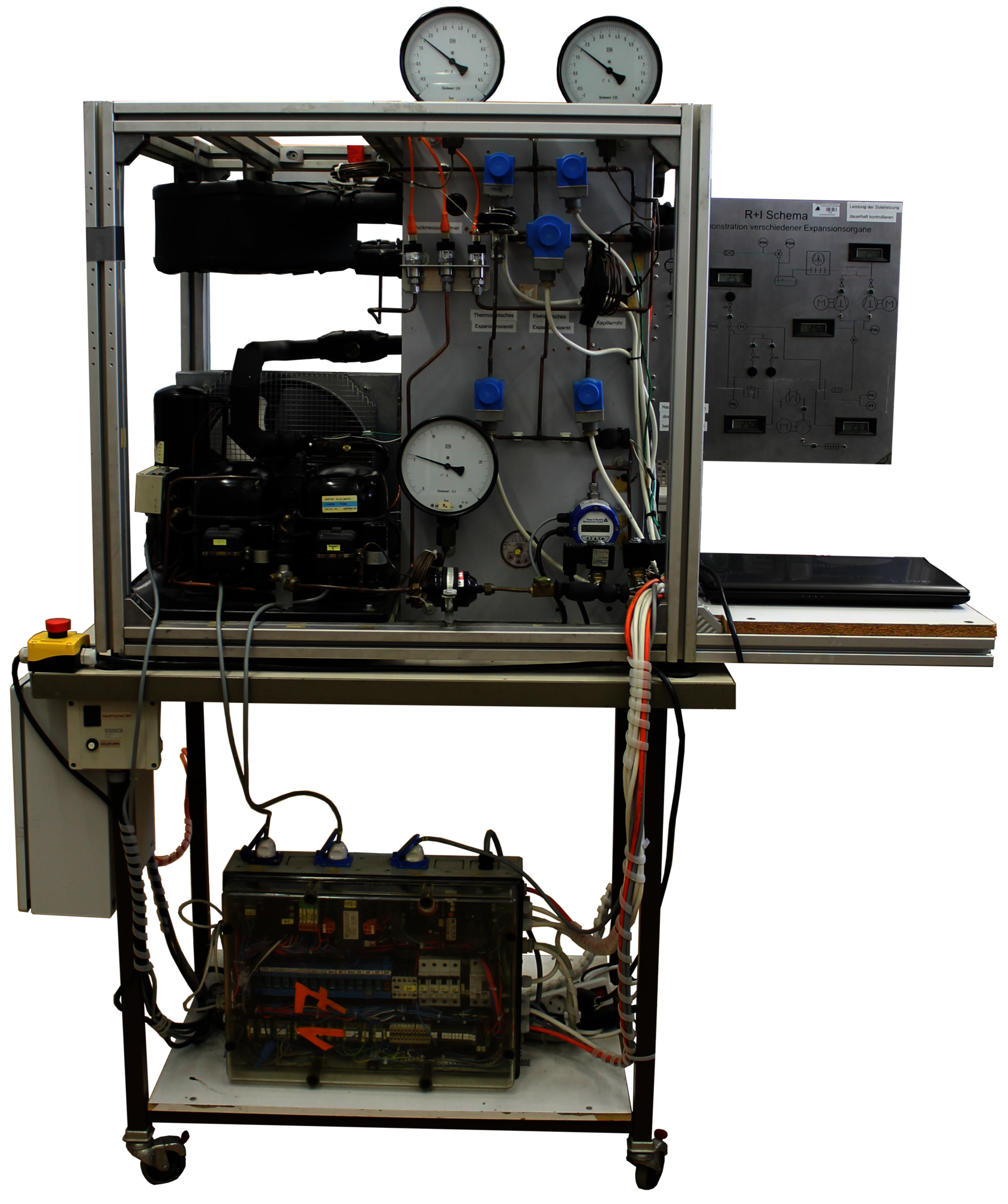
Refrigeration system with different expansion elements
The expansion element is of decisive importance for the quality of a refrigeration system. In this laboratory exercise, the characteristics, advantages and disadvantages and the resulting areas of application of various expansion elements are to be worked out on a model. A single-stage refrigeration system is available for this laboratory exercise, on which the refrigerant can be expanded with either a
- thermostatic expansion valve with external pressure compensation
- thermostatic expansion valve without external pressure compensation,
- automatic expansion valve with pressure control
- capillary tube
can be relaxed.
The temperature readings and the pressure at the evaporator outlet are recorded and processed for graphical display on the PC. This allows the control behavior of the various expansion organs to be visually displayed as a function of time.
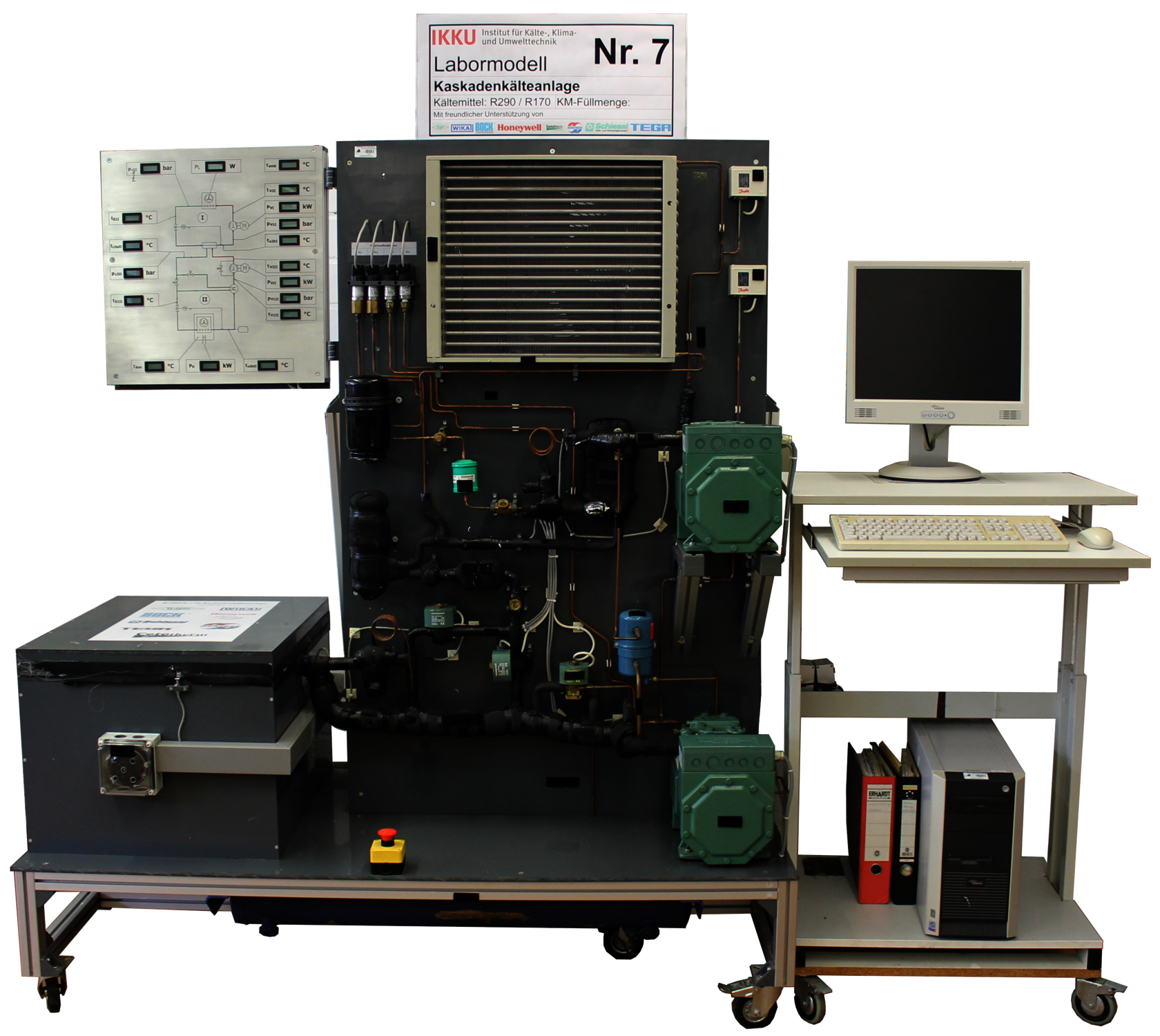
Cascade deep-freeze chiller
With natural refrigerants (R290/R170) for temperatures down to about -80 °C
In order to be able to generate temperatures in the range between -60 °C and -120 °C economically, cascade refrigeration systems are often used. The laboratory exercise is intended to clarify the structure and operating principle of a cascade refrigeration system. For this purpose, four operating points are approached and the associated measured values are recorded. The focus of the evaluation is on the course of the cooling capacity as a function of the evaporation temperature of the second stage. A special feature of the existing plant is the use of hydrocarbons (propane and ethane) as refrigerants.
The control and measured value recording is carried out via a laboratory computer. With the software used, it is also possible to graphically display both circuits in the log p, h diagram as well as the temperature and pressure curves.
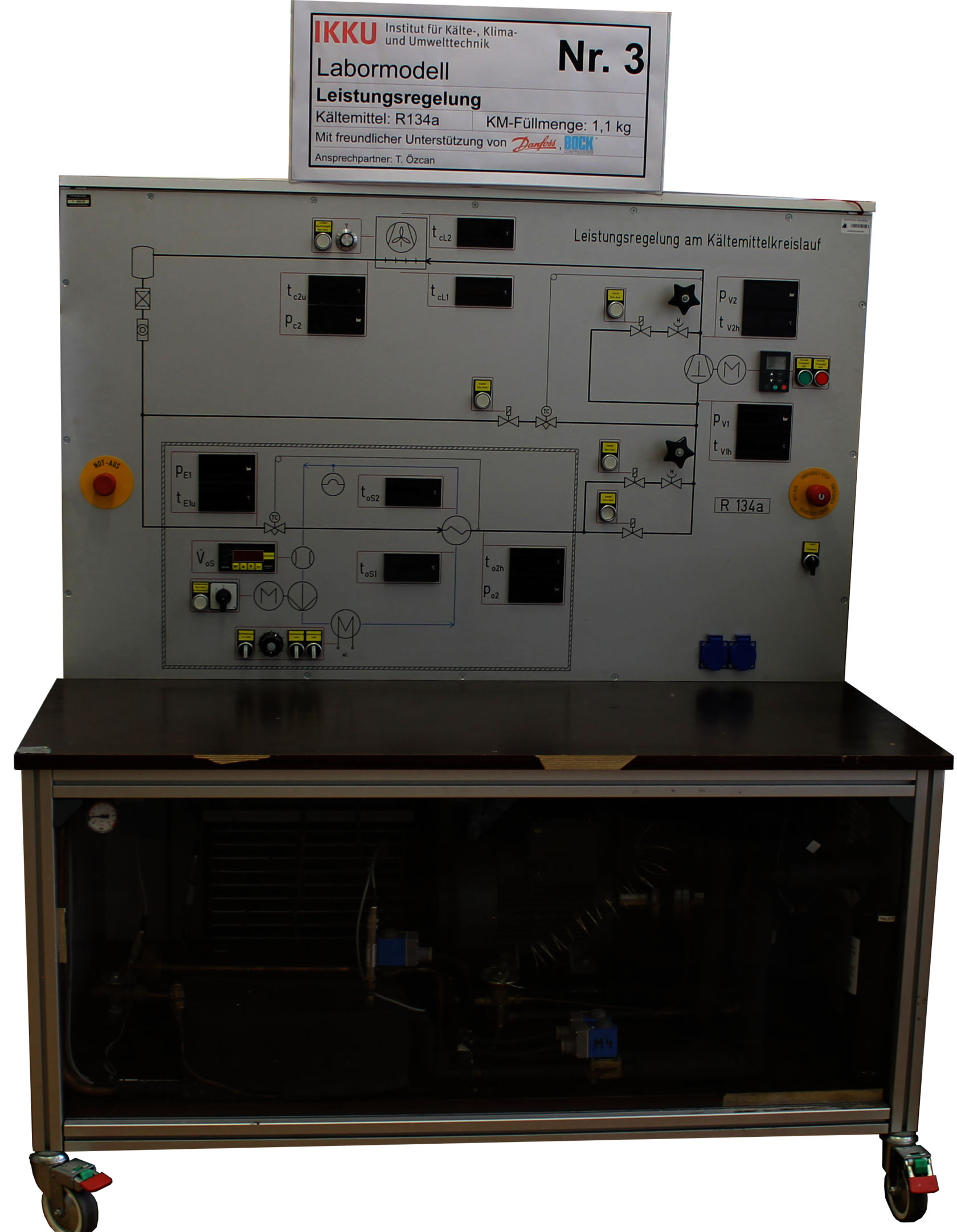
Power control on the refrigeration laboratory model
The laboratory model consists of a simple refrigerant circuit that has four different ways to control the cooling capacity.
In practice, all four of these options are used, but they are very different in terms of their initial and operating costs, their energy efficiency, and their operational reliability.
Based on the data obtained during the laboratory test, it is possible to evaluate each method of capacity control with respect to the above criteria. The refrigeration system has the following control capabilities:
- Frequency converter for stepless control of compressor speed
- Throttle valve in suction line to regulate evaporating pressure
- Hot gas bypass valve to regulate refrigerant flow back to compressor suction port
- Thermostatic evaporator bypass valve for automatic regulation of hot gas superheat at compressor discharge
A new capacity control system using the natural refrigerant CO2 is in progress.
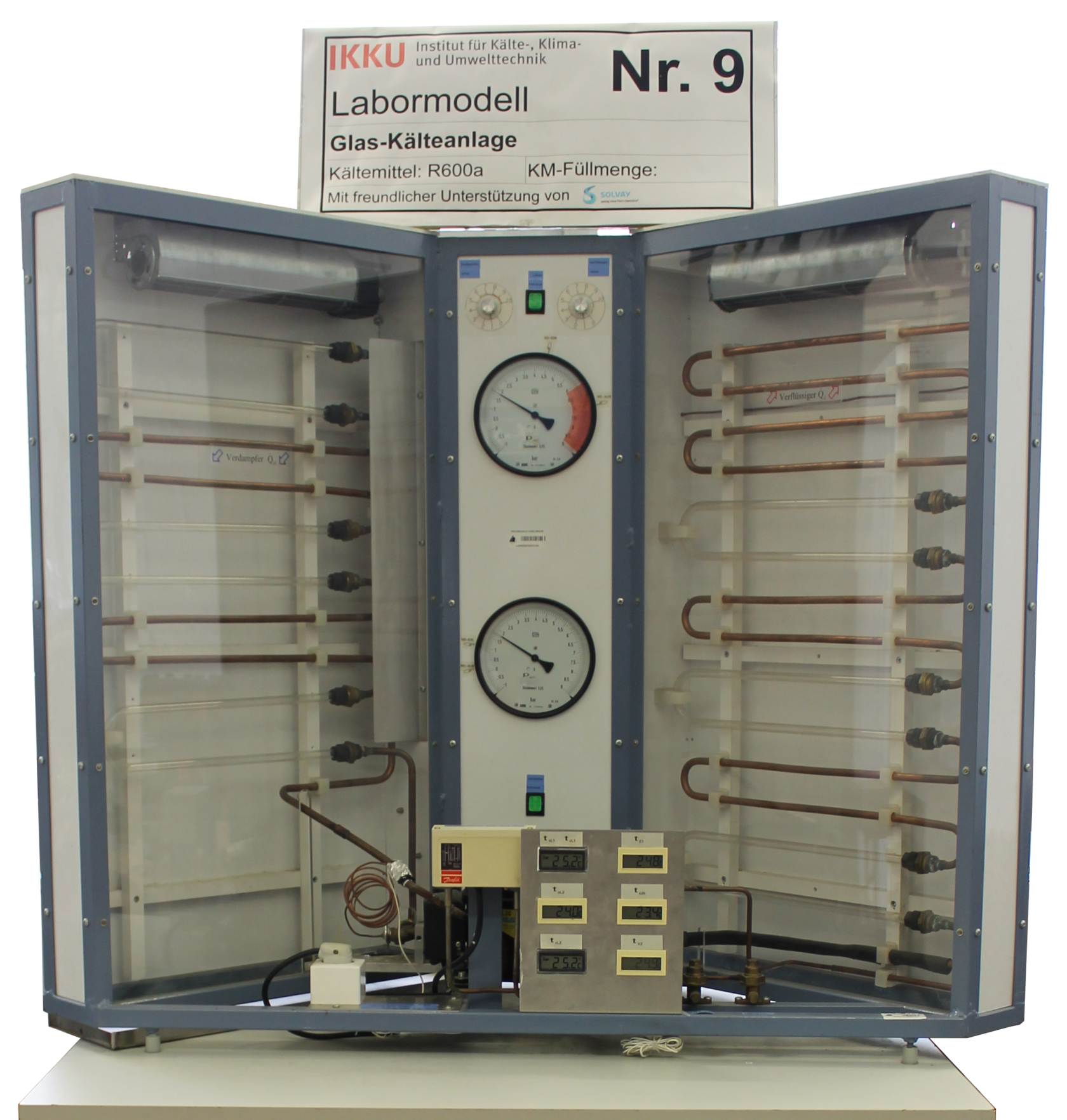
Refrigeration plant with glass heat transfer
To be observed
- Evaporating and condensing refrigerant
- Temperature and pressure in major components
- Condensation of moisture in the air at the evaporator
- Influence of air flow on evaporator and condenser pressure
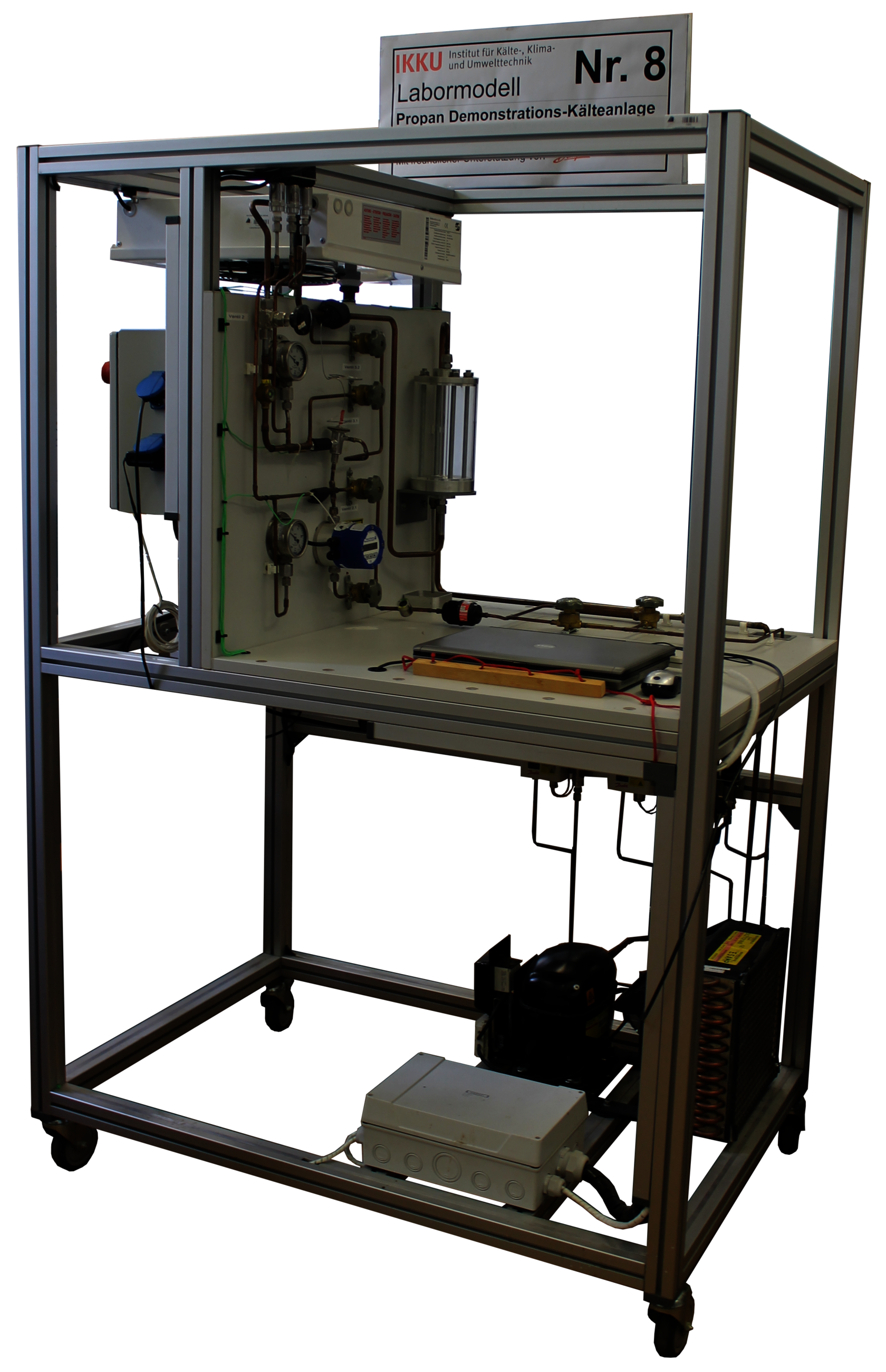
Propane plant for demonstration purposes
The refrigeration system was designed, built and commissioned as part of a bachelor's thesis. For better mobility, it is mounted on a trolley that can be brought to the students in the lecture halls. With the help of extensive measurement technology and the possibility to manually influence the operating behavior of the system, the states of the refrigeration cycle are illustrated in software installed on the laboratory computer. The system is intended to help students of thermodynamics and refrigeration technology to better understand how a refrigeration system works.
Demonstration air conditioner
The knowledge gained in the lecture on air treatment can be reproduced on this system:
- Filtering
- Heating
- Cooling
- Dehumidifying
- Humidify
- Heat recovery
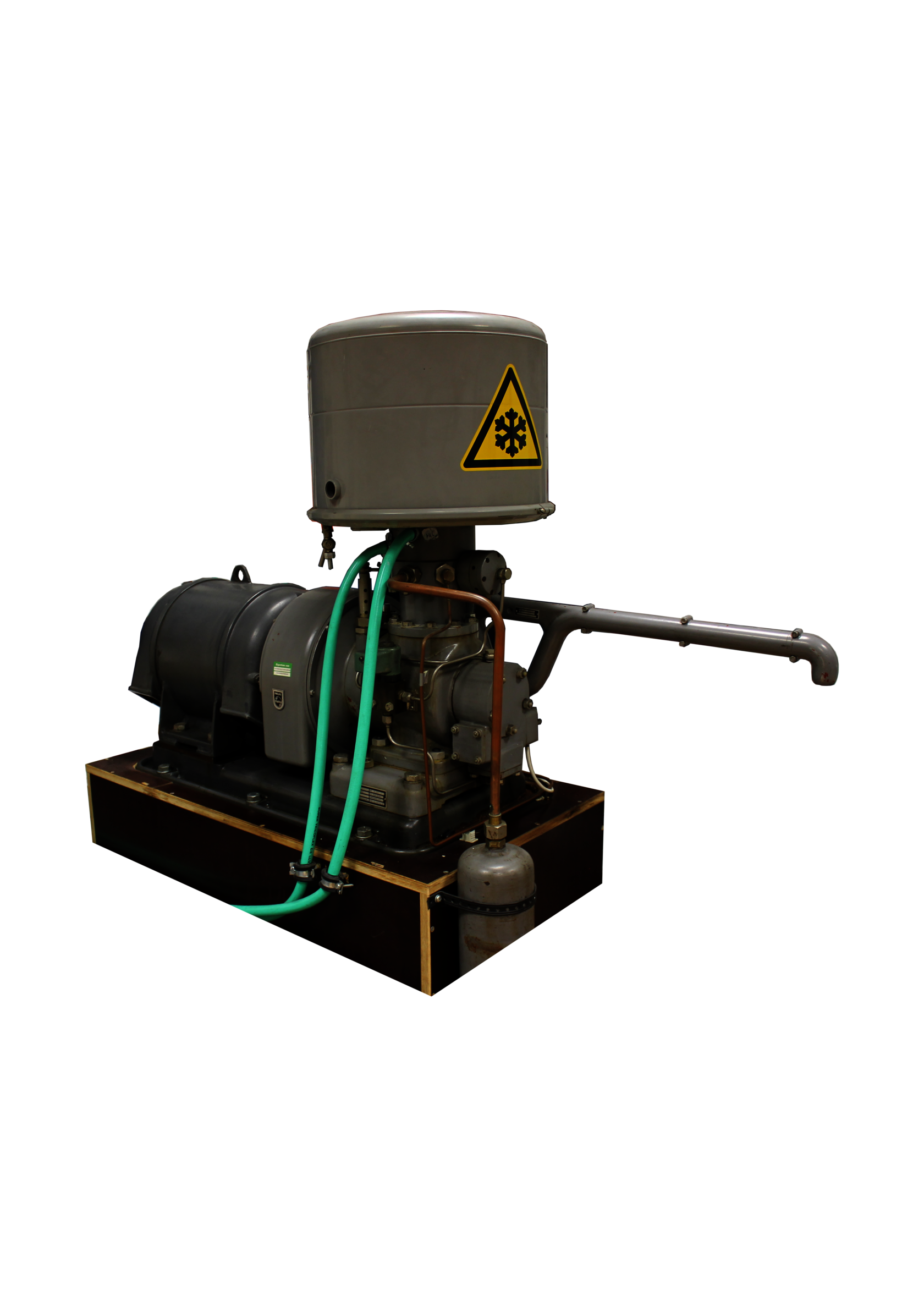
Philipps chiller
After the cold vapor compression chiller and the absorption chiller, the gas chiller ranks third in terms of practical importance or frequency of use. However, this refrigeration machine is specifically used in the temperature range between -80 °C to -200 °C.
In addition to the name cold gas refrigeration machine, the name Philips gas refrigeration machine has become common, because this refrigeration machine was developed by the employees of the Philips company. It represents the reversal of the Stirling hot air process and operates at relatively high efficiency.
Other special features are: no liquefaction or evaporation of the refrigerant (hence the name "gas refrigerator") and no working valves.
The system in the laboratory is used for demonstration purposes and to generate liquid air.
Manufacturer: Philips (Philips Process)
Type: PW 7000
Production: about 5 liters of liquid air per hour
Drive power: 6 kW at a speed of 1450 1/min.
Operating pressure: 25 bar
Working material: 10 g helium
Model for determining the degree of delivery
Compressors (such as gas compressors, air compressors, refrigerant compressors) deliver volume flows at different pressure ratios. If the back pressure or discharge pressure of the compressor increases, the discharge capacity of a compressor decreases. This is one of the main reasons for moving from single-stage to two-stage or multi-stage compression above a certain pressure ratio.
The ratio of actually delivered volumetric flow to theoretically possible volumetric flow is called volumetric efficiency. It is in the range of 0.6 .... 0.9 for designed systems.
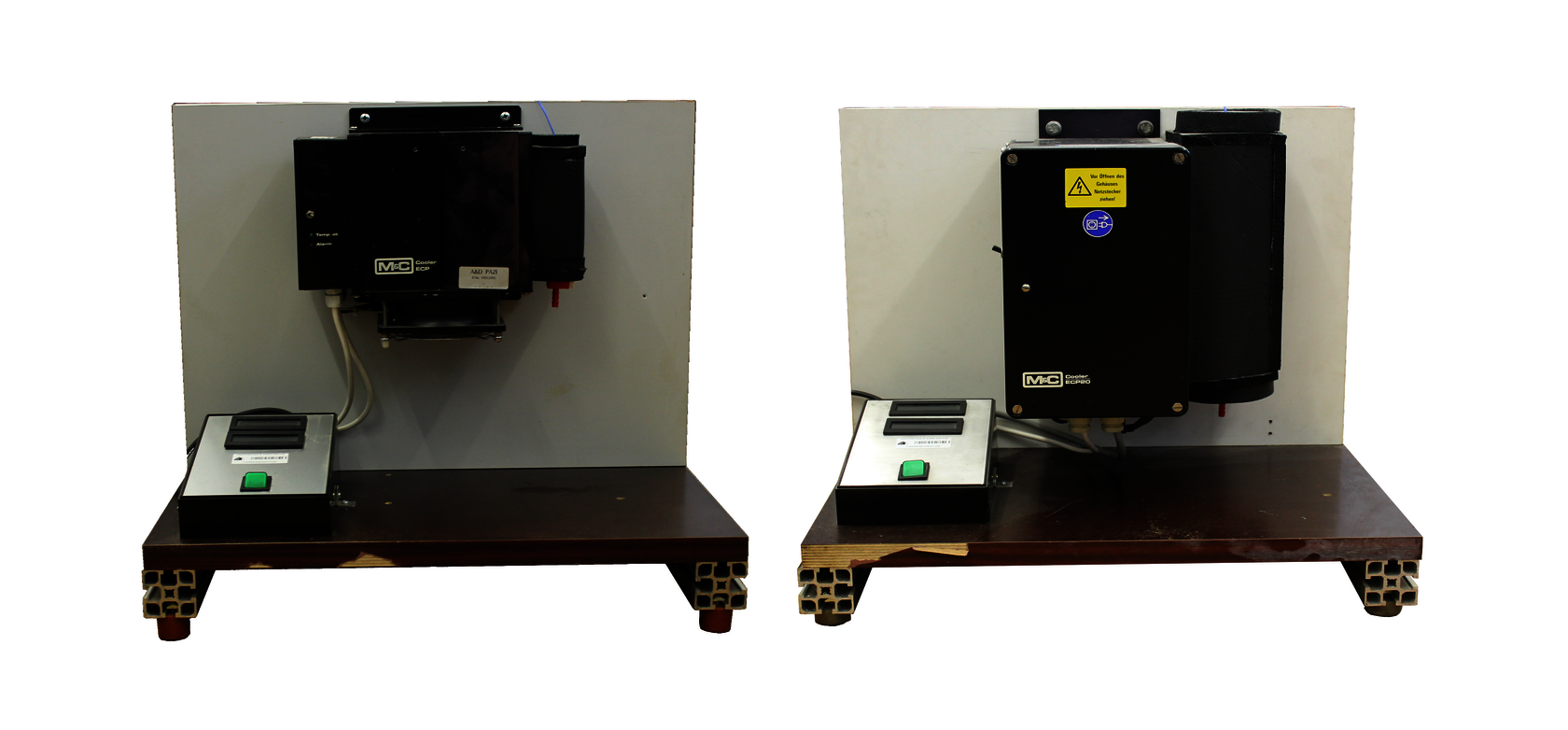
Thermoelectric cooling with Peltier elements
Peltier elements are used for cooling in the following requirements:
- precise point cooling
- good controllability
- free from vibration and / or low noise operation
- easy switching between cooling and heating
- narrow or angled installation conditions
Two plants are available to carry out the experiment. At each of them, the cooling coefficient of performance of Peltier cooling is to be determined.
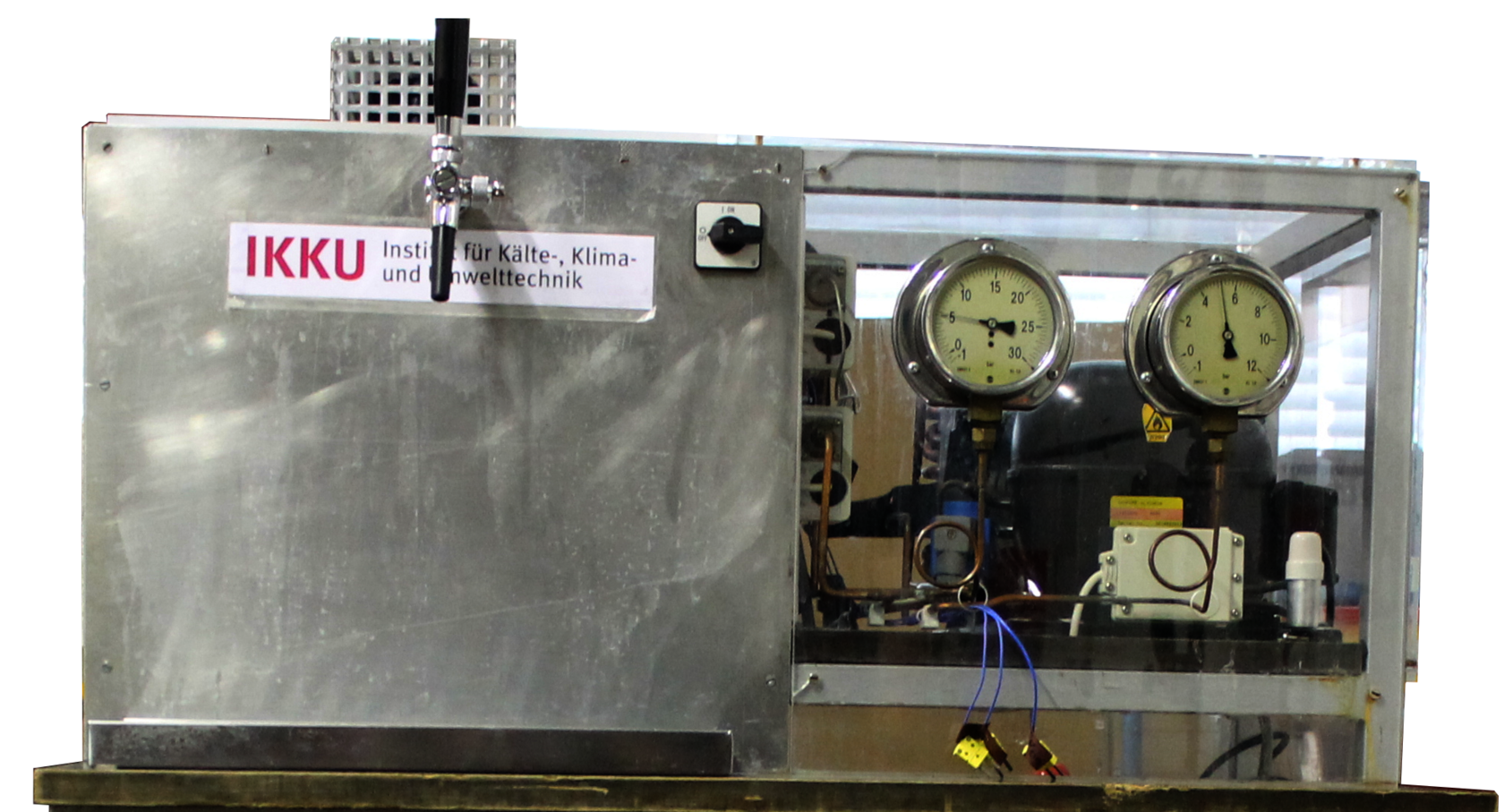
Beer cooling plant
The cooling of food is the largest application area of refrigeration technology. This experimental model was designed and built as part of a diploma thesis.
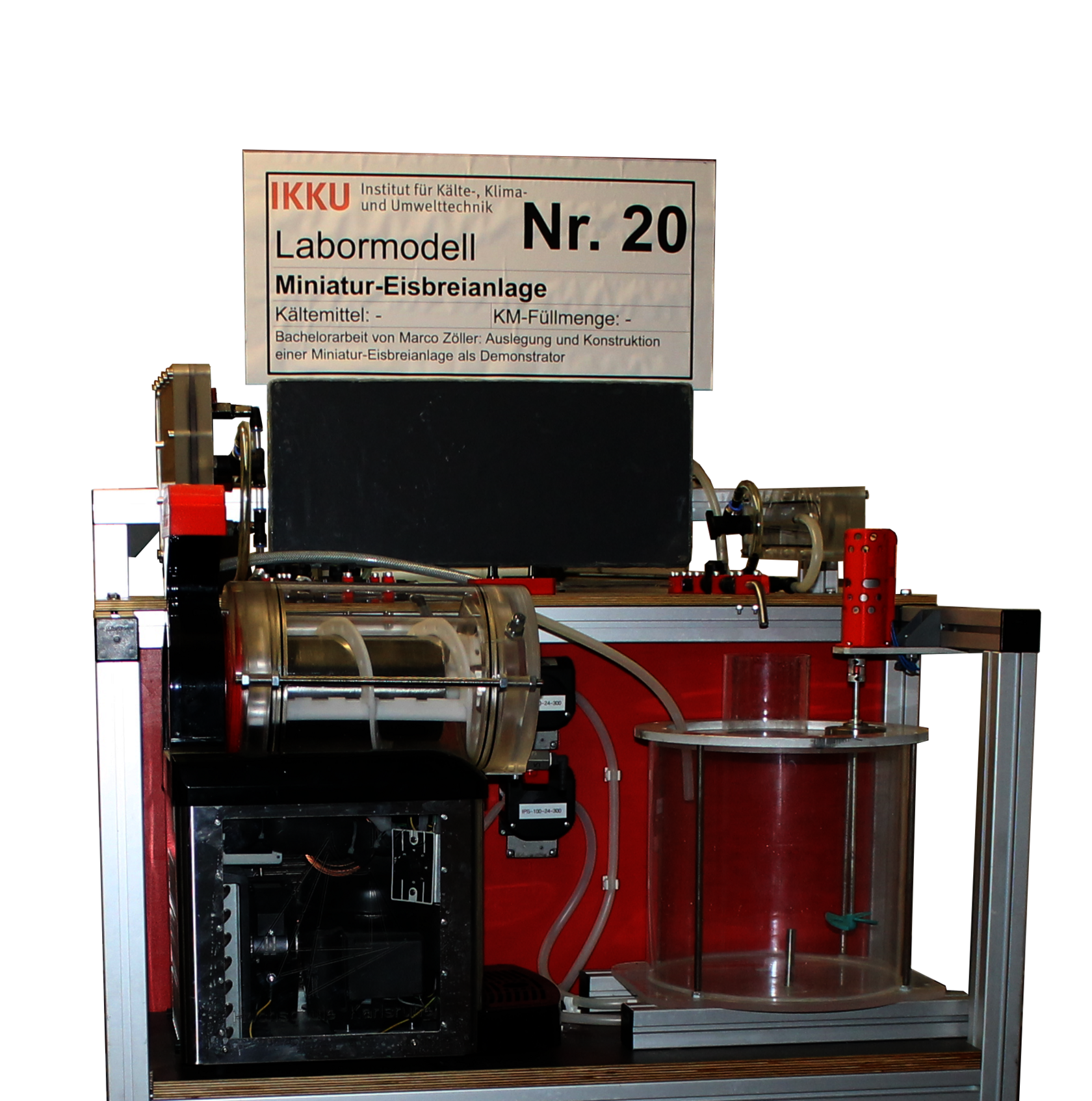
Miniature icebreaker
The topic of icebreaking represents a major area of research at Karlsruhe University of Applied Sciences, and is one of the core competencies of the Institute of Refrigeration, Air Conditioning and Environmental Engineering. Although there are some industrial-scale ice slurry production plants in the laboratories, they are not permanently available to the students as demonstration objects due to ongoing research activities. For this reason, this miniature icebreaking plant was designed and constructed as part of a final thesis. A converted slush ice machine from the catering industry is used as the ice maker. In the context of this thesis comprehensive work concerns the modification of the slush ice machine, as well as the complete construction of all other components such as machine frame, ice storage, agitator, consumers such as heat exchanger and the piping and hose system with the valves.
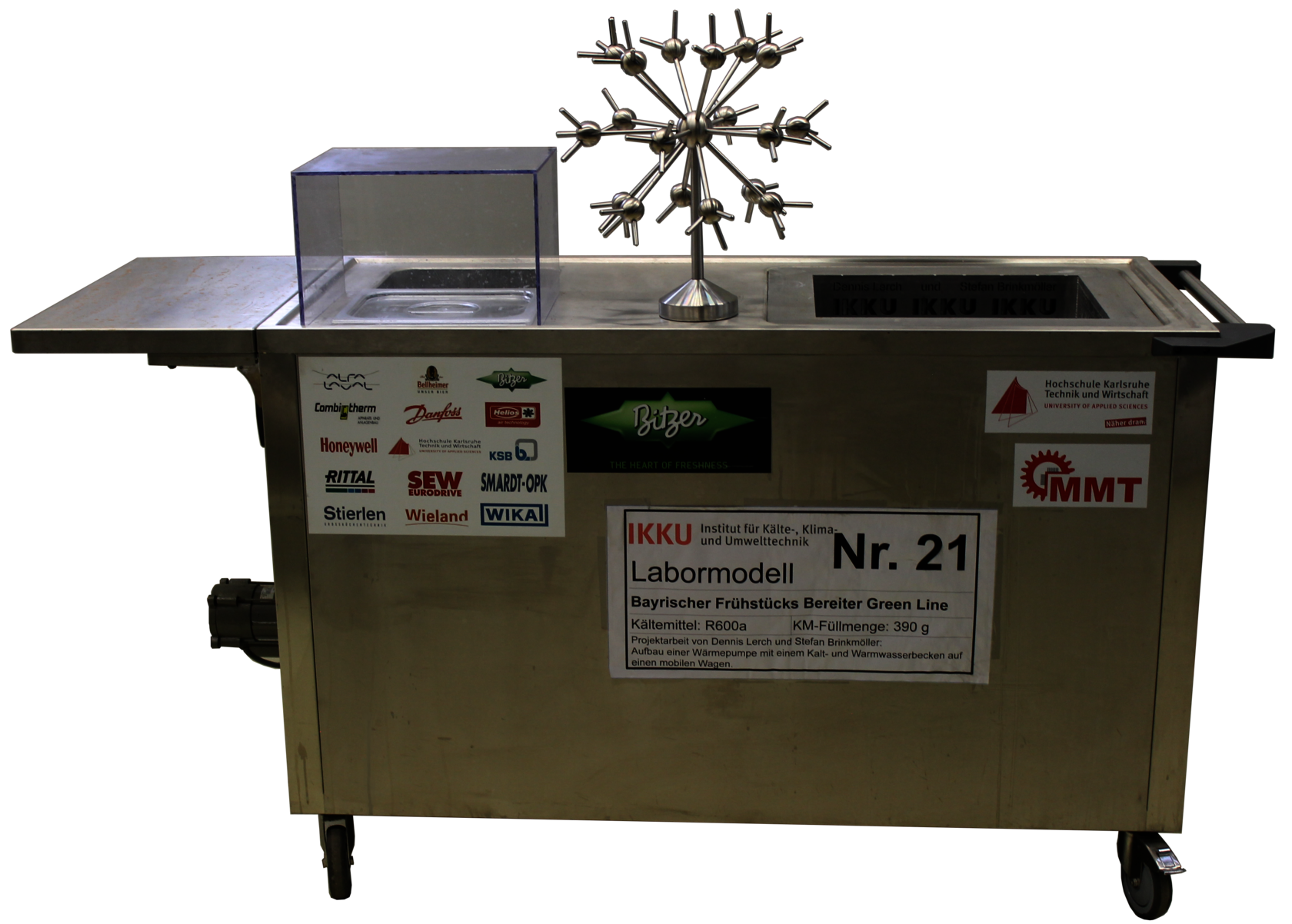
Bavarian breakfast trolley
As part of the project work "Design of a mobile high-temperature heat pump", the "Bavarian breakfast maker Green Line" was developed at Karlsruhe University of Applied Sciences in the summer semester of 2016. The result of this project work became a demonstration object for the Refrigeration, Air Conditioning and Environmental Engineering course.
But what exactly is the "Bavarian Breakfast Maker Green Line"? It is - simply put - a heat pump that has the task of cooling beer on one side and heating white sausages on the other. The heat pump is located in a cart designed according to gastronomic hygiene guidelines to work with food.
The heat source is a water basin that can hold 34 NRW bottles of wheat beer, plus about 40 liters of water. The water serves both as an energy source and for better heat extraction from the bottles, so that they get cold faster. The heat pump is designed to cool the water, including the glass and beer, from 20 °C to 5 °C within 60 minutes. The energy extracted is released into the hot water tank via the refrigeration circuit together with the compression energy. There are about 12 l of water and 46 pieces of white sausages, which are heated from 20 °C to 80 °C.
Heat pump
The aim of this thesis was to build and commission an electrically driven, switchable heat pump for exergetic analysis in laboratory operation. The exergetic analysis is a method for efficiency assessment. It enables generally valid formulations about the quality of the work process and shows where exergy losses occur in a system.
After the exergy-relevant measured variables have been established, a large number of sensors are selected, procured and installed for the air-to-air cold-steam compression heat pump provided by the Daikin company. The split system equipped with measurement technology uses R410A refrigerant. The system can meet a heating demand between 1.3...4.5 kW, depending on ambient conditions. In cooling mode, under typical summer conditions, 1.3...3.0 kW of heat can be removed from the living space. Switching between the heating and cooling modes is performed by a four-way valve, which causes a circuit reversal of the refrigerant. A radiator is located on the indoor unit in parallel with a finned heat exchanger, which is designed to contribute to comfort in the living space by emitting radiant heat during heating operation.
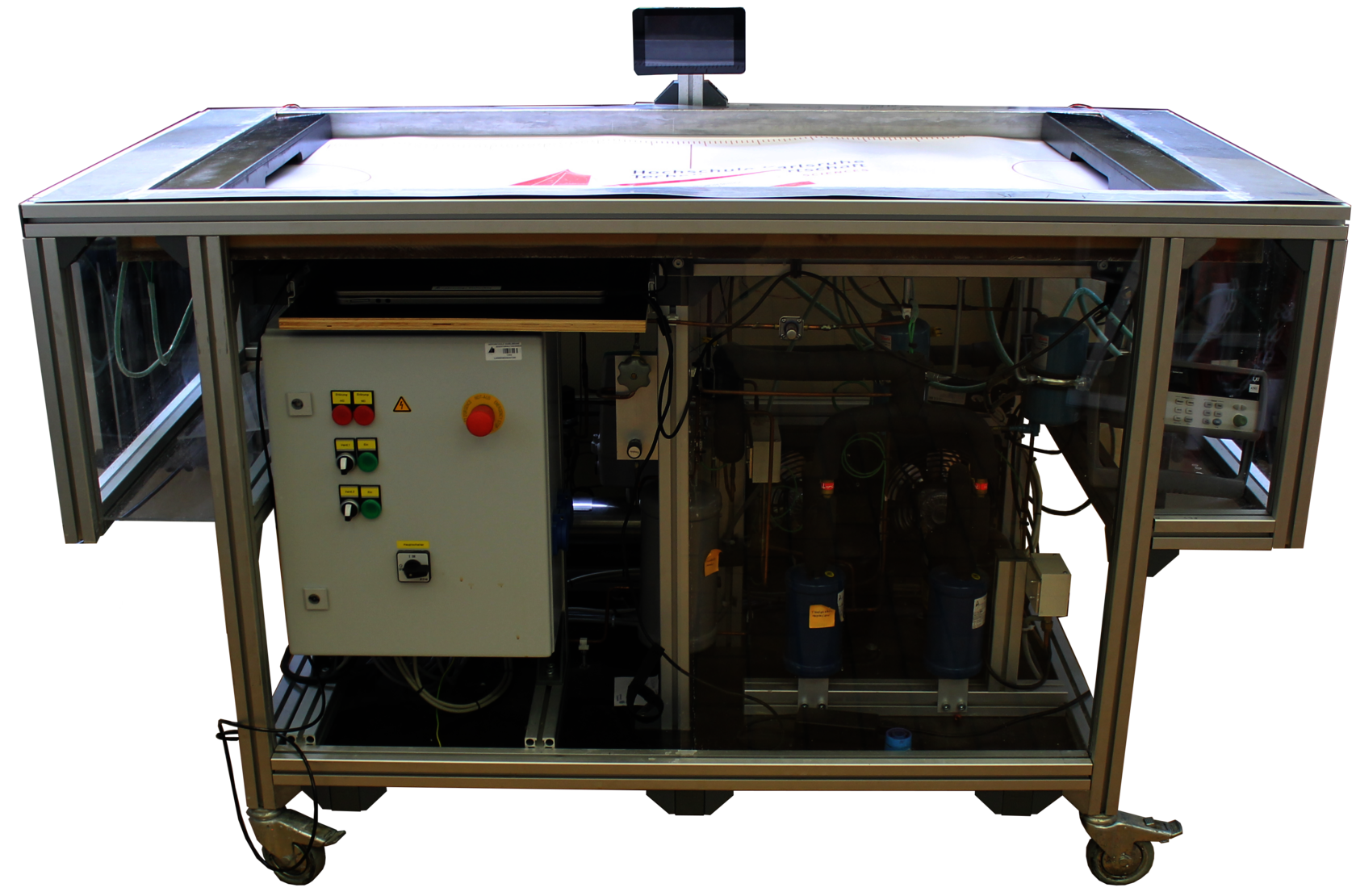
Ice hockey rink
The plant was designed, constructed, built, and commissioned as part of project work and final theses.
Students use this plant to investigate the energy efficiency of a heat-pumping compression machine in transient operation - experimentally.
A detailed exergetic analysis shows in which components an increase in efficiency is promising.
Ice area: 1.5 m x 0.76 m
Construction refrigeration system
Parallel system with two refrigerant compressors
Continuously adjustable hot gas bypass valve
Evaporator made of connected copper tubes
Condenser with pressure-controlled (refrigerant pressure) airflow cooling
Operation
Cooling operation: production of the ice surface in about 3 h with 1000 W cooling power
Playing operation: ice is kept at a constant temperature over a wide area
Measurement technology
16 x temperature: playing field
12 x temperature: refrigerant circuit
6 x pressure: refrigerant circuit
2 x electr. power: compressors and fans
1 x Coriolis mass flow meter