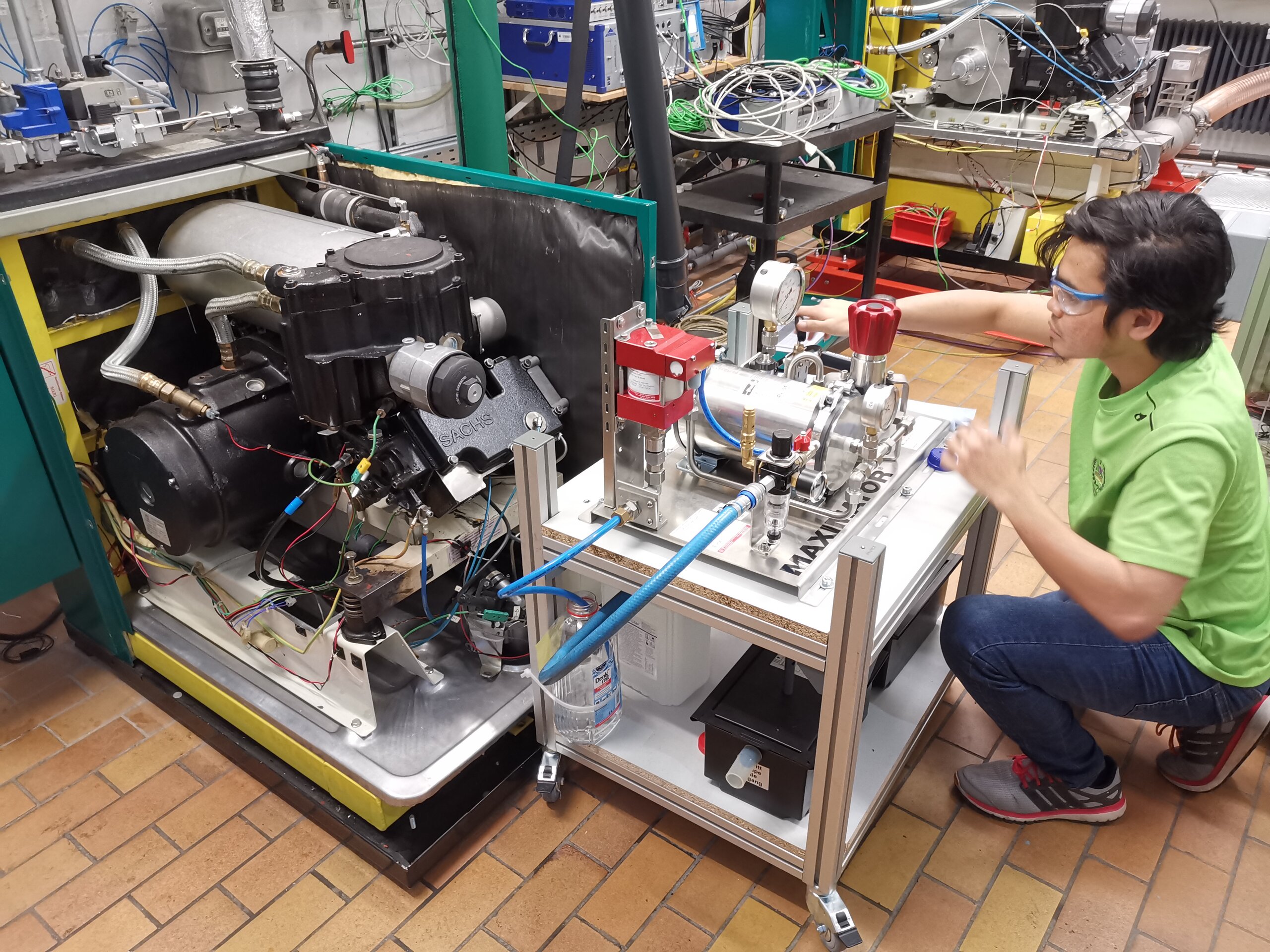
LiquidEGR
LiquidEGR
Most CHP natural gas engines are lean burn. Lean operation is characterized by high efficiency and cold combustion, which enables compliance with NOx emissions. Due to the increasing number of CHP units in Germany, stricter NOx emission limits are expected. Aiming at the new NOx limits by further leaning the mixture might be possible. However, this will certainly lead to a deterioration of the efficiency (red area in the diagram, Figure 1).
![[Translate to English:] Einfluss der Wassereinspritzung auf den Zielkonflikt zwischen Motorwirkungsgrad und NOx-Emissionen](/fileadmin/Hochschule_Karlsruhe_HKA/Bilder_WE-IKKU/GenLab/HKA_WE-IKKU_Imagefoto_GenLab_LiquidEGR_01.png)
Water injection can be used as an alternative here. An efficient water injection system enables effective cooling of the intake mixture without compromising engine efficiency. To achieve this, two criteria must be met: Highest possible atomization of the injected water and minimum water wall wetting. Due to mixture cooling, the geometric compression ratio can be increased without reaching the knock limit. This leads to a further increase in the thermal efficiency of the engine. The water needed to cool the mixture is recovered from the engine's exhaust gas by an external heat exchanger.
The project involved three main phases:
In the first phase, the system of condensate water recirculation was investigated. The focus was on the injectors to be used, high-pressure injection system (for high atomization) and the external heat exchanger made by Bomat to recover the condensed water from the exhaust gas of the engine.
The second phase of the project dealt with the intake manifold water injection both experimentally and numerically (3D CFD simulation in AVL FIRE). In the experimental investigations, variations on injection timing, injected water quantity, combustion center of gravity position and compression ratio were performed and their influence on mitigating the target conflict between engine power, efficiency and NOx emissions was evaluated. The 3D CFD simulations provided a better understanding of the interaction of the fuel injection process with flow, wall film formation, evaporation, and combustion.
In the final phase of the project, the direct water injection system was also studied experimentally on the engine test bench and numerically in 3D CFD. The engine cylinder head was machined to perform the engine experiments. Thus, further research topics on gasoline or renewable fuel direct injection can be investigated on the engine test bench. With direct injection, larger variation ranges of injection timing and injection pressure difference are possible compared to intake manifold injection.
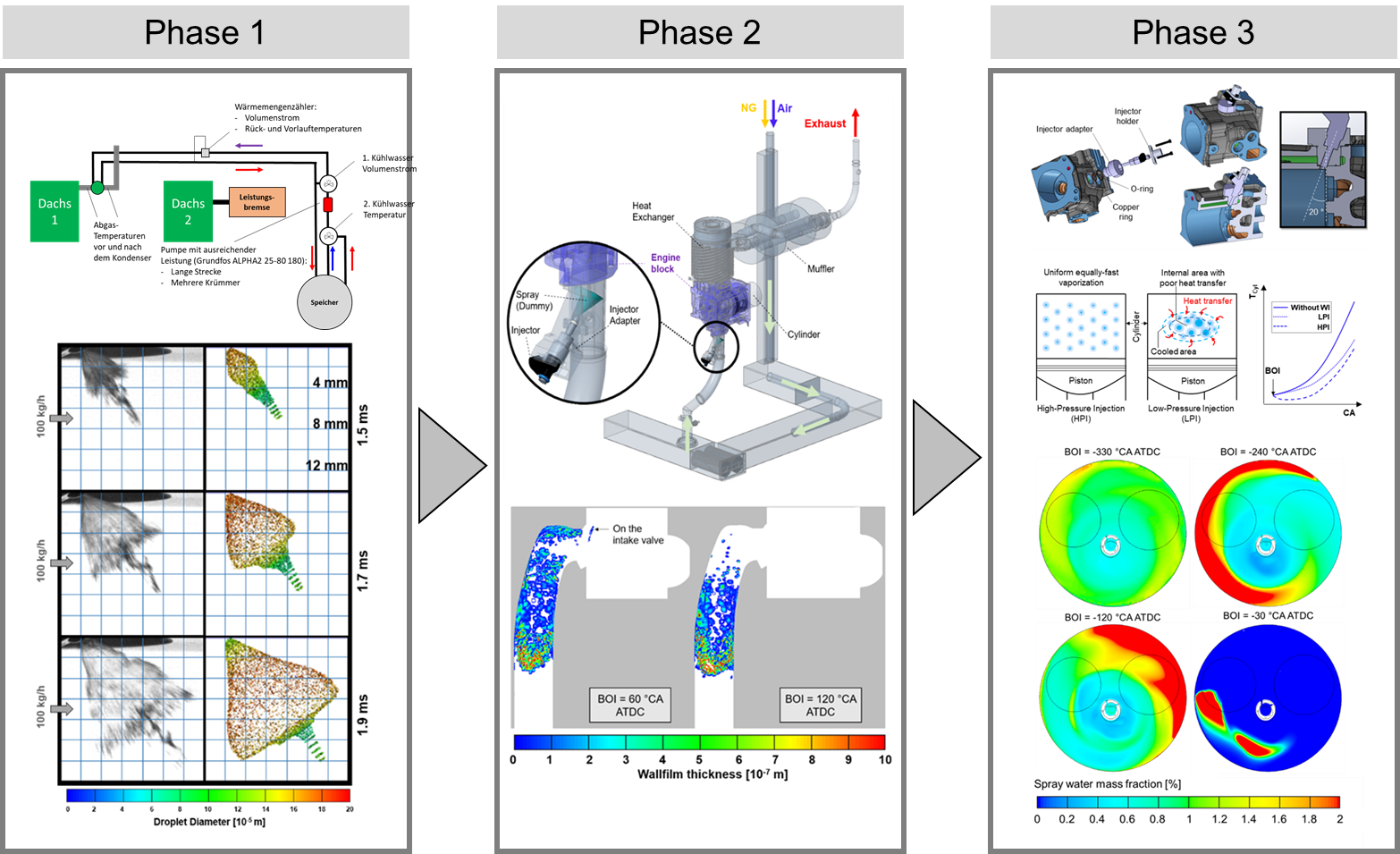
Current information about the project
The expertise and knowledge gained in the field of water injection and water recovery from exhaust gas will be used in current and future research projects (LeanStoicH2, EGRreact) will be further applied and developed.
Verwandte Publikationen
- Beltaifa Y, Judith J, Kettner M, Eilts P, Klaissle M, Wiersbitzki V: Intake Port Condensed Water Injection for a Clean Natural Gas Engine : Strategies and Restrictions. In: Bargende M, Reuss HC, Wagner A (Hrsg.): 20. Internationales Stuttgarter Symposium 2020 : Automobil- und Motorentechnik. 20. Internationales Stuttgarter Symposium 2020 (Stuttgart Vieweg, 17.-18.03.2020), Wiesbaden: Springer 2020 (Proceedings), S. 499-518.- ISBN 978-3-658-29942-2 (Elektronische Veröffentlichung: http://dx.doi.org/10.1007/978-3-658-29943-9_38)
- Beltaifa Y, Kettner M, Eilts P, Klaissle M: Impact of Intake Port Water Injection Timing on Mitigating the Tradeoff between Performance and NOx Emissions for a Naturally Aspired Micro-CHP-Engine. In: SAE Technical Papers, ISSN 0148-7191 (2020), 14 S. (Elektronische Veröffentlichung: https://saemobilus.sae.org/content/2019-32-0576/)
Projectpartners
SENERTEC
BOMAT GmbH
Bundesministerium für Bildung und Forschung
Last updated
26.03.2021