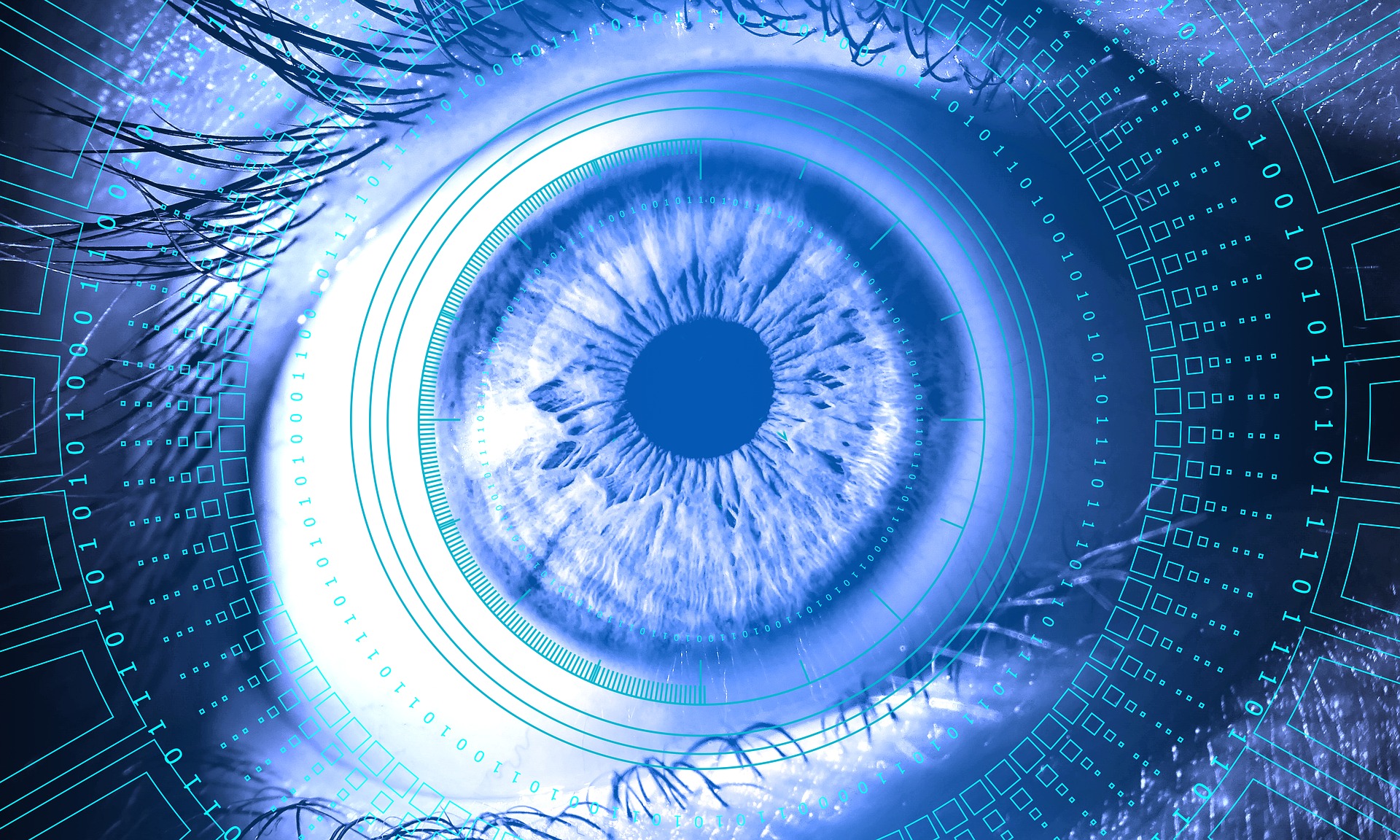
QualiTED
QualiTED: Autonomous, mobile system for intelligent linking of production workstations with transport-parallel quality assurance
Context
Modern production focuses increasingly on flexible material flow systems such as automated guided vehicles (AGVs). These systems are often supplemented by robotic arms to reduce the workload of workers by carrying out various tasks, especially those that are monotonous or dirty. This also improves quality, as typical errors resulting from these monotonous tasks do not creep in with a robot. The factory of the future demands such high mobility and flexibility. Static production lines will be replaced by the next generation of robots.
For small or medium-sized series in traditional mechanical engineering, the use of mobile robot systems is currently not economically viable. Individual production steps are still interlinked by rigid continuous conveyor technology or manual transport. Especially in areas with a high number of variants, these rigid systems or manual transport between individual production stations are difficult and often lead to errors. Automated interlinking for smaller series will help the broad range of medium-sized companies in particular to position themselves better against their large competitors.
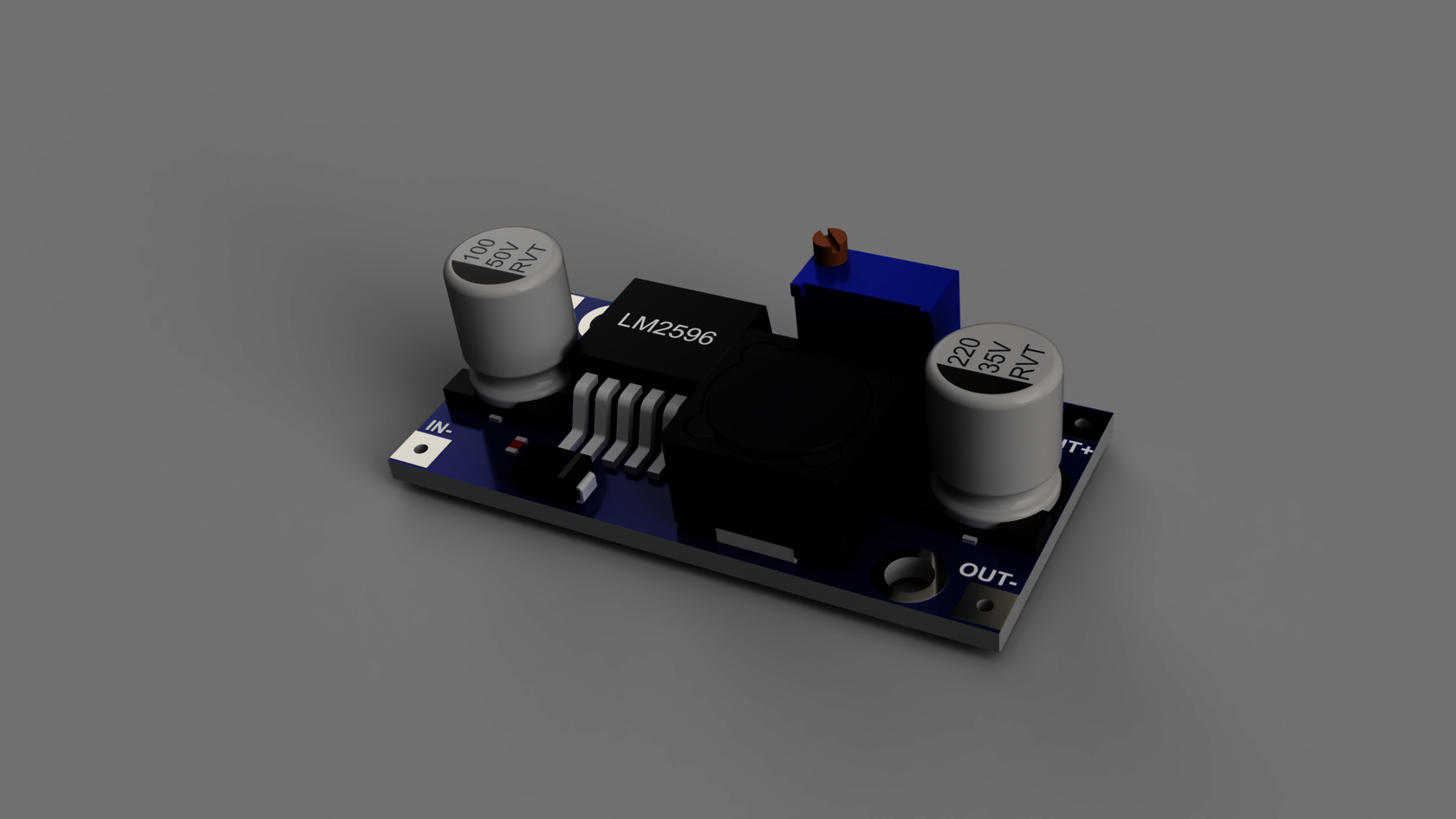
Project goals
The goal of the QualiTED project is to develop an autonomous, mobile system that can be used for intelligent linking, documentation and optimization of production processes. A production chaining of directly adjacent production steps with short distances or a cross-hall chaining of individual production steps will be possible with a new type of vehicles. The resulting transport times will be used to carry out quality-assuring image processing in parallel.
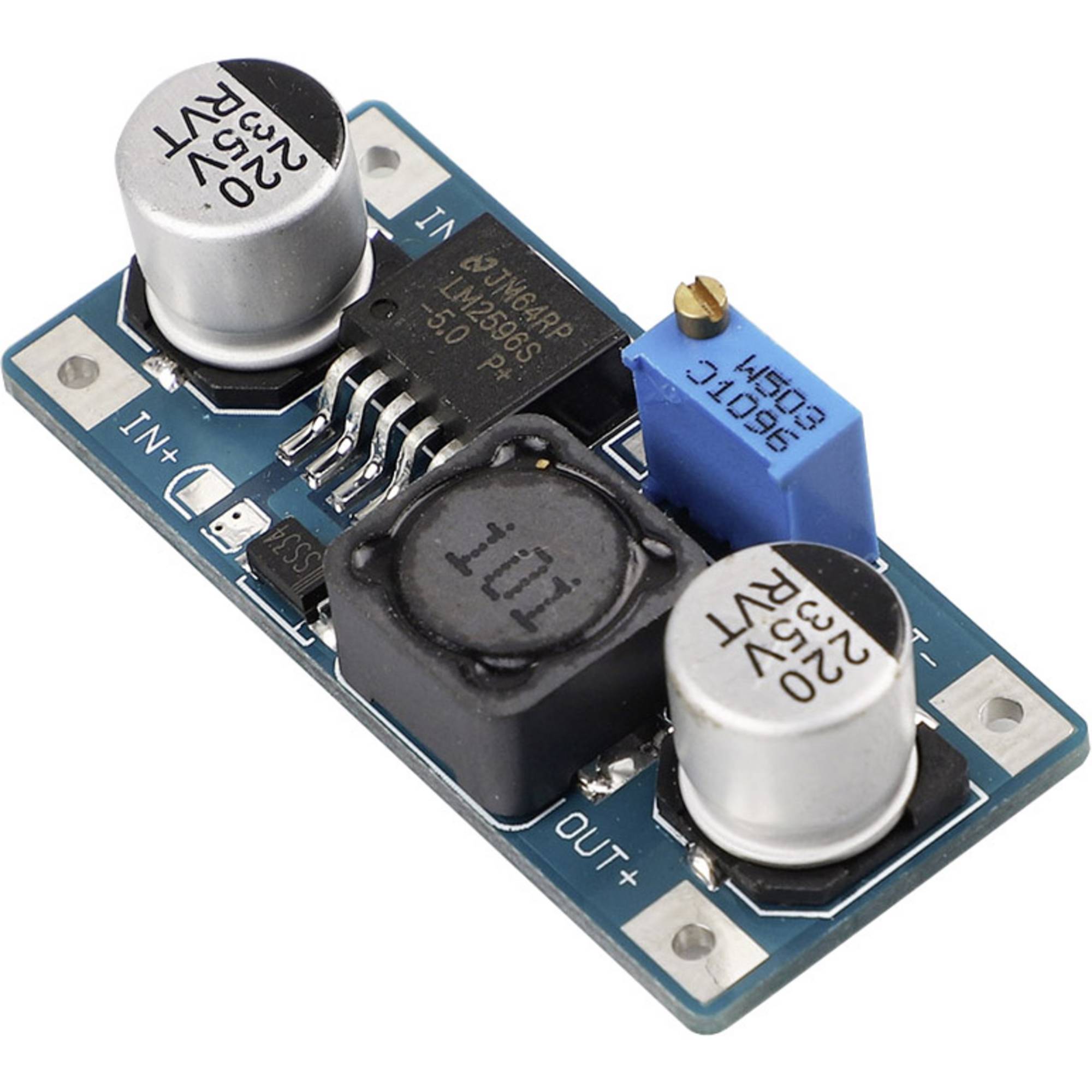
Therefore, the system has to be able to react intelligently to a changing environment. AI-based image allows a classification of (in)traversable surfaces and environments. The classification scheme will finally be analyzed and improved by using deep neural network visualization techniques (Deep Learning). This process will be realized by using synthetic image data via transfer learning, as well as an energy-saving embedded hardware.
Methods
In the framework of the project, a camera system is used for process monitoring and quality assurance. This measuring system will provide a check of production and manufacturing steps. Sensors detect and control the exact position of the workpieces. In addition, the system enables quantity counts and weight checks as well as their evaluations. Quantity, weight and workpiece position are continuously recorded. If errors are detected, direct delivery is made, for example to stations for reworking.
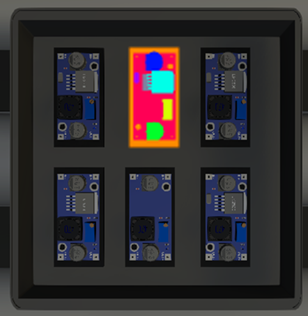
To achieve high precision while maintaining robustness and affordability of the system, a toolbox developed at Karlsruhe University of Applied Sciences based on the Unity3D rendering engine will be used and further developed to create synthetic training data. The existing visualization techniques (e.g., Grad-CAM) will be further developed and investigated for use in complex tasks such as object recognition in order to enable users to interpret the decisions made by the learning system. On the one hand, the visualizations permit the systematic detection of structural errors. On the other hand, they enhance the comprehensibility of the learned algorithms and thus increase the confidence of potential customers in the system.
Status
Ongoing project 02/2021 — 07/2023
Partner
Contact
Project manager
Prof. Dr.-Ing. habil. Björn Hein
Phone: +49 (0)721 925-1942
bjoern.hein
@h-ka.de
Project funding
The QualiTed project is funded by the German Federal Ministry for Economic Affairs and Climate Action (formerly: BMWi) as part of the Zentrales Innovationsprogramm Mittelstand (ZIM, Central Innovation Program for SMEs)
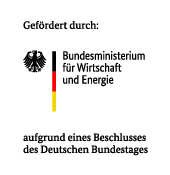